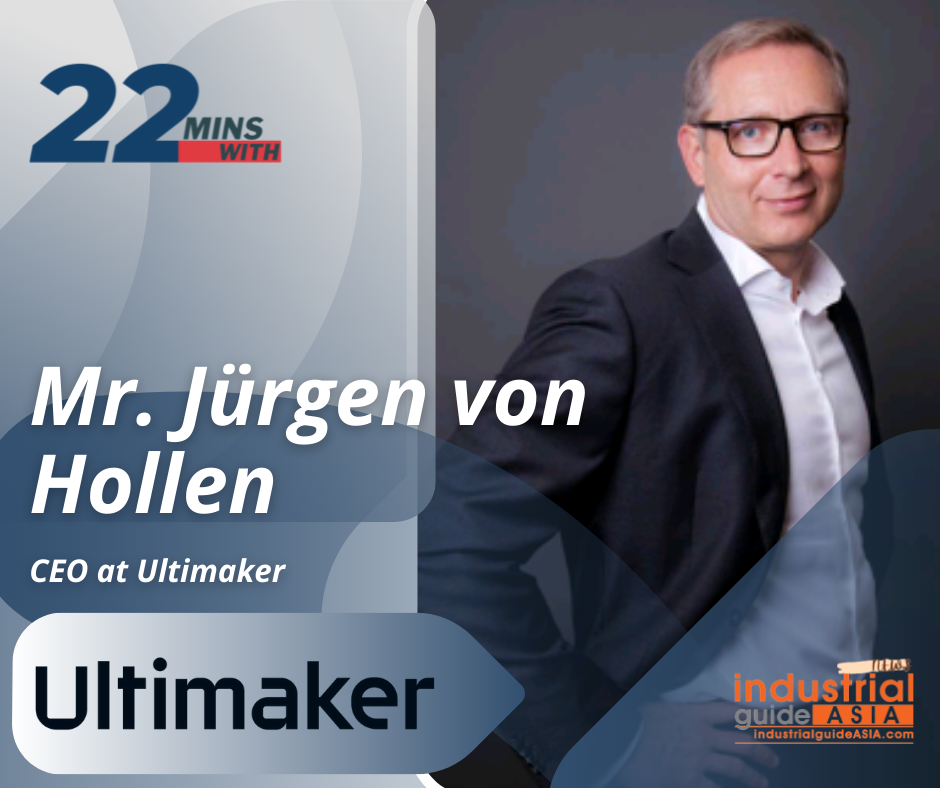
Mr. Jürgen von Hollen - CEO at Ultimaker
1. What is the possible future in the printing industry after the Pandemic?
Increasing volatility in global markets driven by events such as the current pandemic highlight the need for businesses to increase the flexibility of their operations. 3D printing technology can help every company – large, medium, or small – stay on top of their supply chains and keep innovating anywhere, anytime. Flexibility, customization, and specific, scalable solutions are key to maintaining a strong foothold for any company in a pandemic-stricken world. These are also areas in which additive manufacturing has both a notable advantage and a positive effect on the wider adoption of 3D printing, post-pandemic.
At Ultimaker, our plan is to accelerate the concept of providing companies with a solution, not just a printer. We do this with a new ecosystem approach that gives users a cloud-based platform to access our software, education, Marketplace, library, and services. Network functionality enables remote monitoring, so Ultimaker engineers can troubleshoot any issues from anywhere at any time. The Ultimaker platform offers businesses an end-to-end workflow, from enabling engineers to collaborate on a design, to storing applications, and printing on demand. We enrich the platform with our ecosystem of partners to contribute to their areas of expertise, and our open platform to enable companies to push the boundaries. Each company has unique processes, needs, and timelines, and we don’t want to offer them just one solution, but a whole platform to customize that solution.
Ultimaker now bundles all new 3D printers with Ultimaker Essentials. For companies that wish to further scale and professionalize their 3D printing activities, Ultimaker also launched two new software plans:
Ultimaker Professional, which helps professionalize 3D printing innovation through collaboration and advanced software. AndUltimaker Excellence,a complete and custom solution aimed at accelerating the business’ digital transformation.
Ultimaker Excellence offers open interfaces, APIs, consultancy, and other tools for companies and developers to further innovate and make it happen.
2. How your company ensure the environmental sustainability during this time?
Companies worldwide are currently considering the complete workflow in regard to pollution and carbon footprint. 3D printing can be a strategic change maker in this process to work in line with their strategy of running a greener factory.
One solution in which 3D printing can make a difference is, for instance, that creating, storing, and sharing files digitally helps to reduce your carbon footprint, since less needs to be shipped from A to B. Furthermore, there is an opportunity here to reduce the amount of waste. Because you’re producing only what you need – where and when you need it – you’re reducing the amount of potentially unused stock parts. And collaborating on designs and prints with colleagues across the globe has never been easier, with our recently launched software plans. This helps speed up the innovation process and helps companies that are working on sustainable solutions to go from concept to prototype much faster. A simple tool printed to reduce the number cans falling from a production belt, thus less waste, can make a small but significant impact.
Furthermore, thanks to our open ecosystem, customers can select from the widest range of filament available, including recycled filament – for instance Fishy Filaments, which is made from old fishing nets.
3. What are the new trends that customers can look forward in the printing industry?
The rise of digital warehouses, in which customers will centrally store and share designs throughout their locations. The new Digital Library, which is hosted in the cloud, allows for collaboration and application development among teams, and is a secure place to house your digital part inventory. The reporting and analytics tool provides useful insights into the usage of individual printers, print fleets, projects, and applications. It’s designed to provide a full oversight of your entire 3D printing operation, while reducing costs with robust data on costs per part, material usage, and more.
4. Are there any exciting developments coming up from your side?
At the recent the Ultimaker Transformation Summit, we announced Ultimaker’s transformation, from a product to a platform company, to drive innovation and growth globally. We are uniquely positioned as a leader in the professional 3D printing segment, delivering both hardware and software solutions. We will ensure this platform stays future proof, stable, and flexible to enable the development, nurturing, and orchestration of ecosystem products and services, including hardware add-ons, materials, and software. Our belief is that all businesses should have the opportunity to take advantage of the platform and ecosystem. This allows them to remain flexible and productive in a volatile world.
5. What is the next technology disruption that you foresee in this sector?
The expected global market growth for 3D printing is, depending on market research, between 20-30%.
MGC:
Further elimination of the typical barriers for adopting 3D printing will have a big impact on the sector; there is still much that can be done to reduce the complexity of getting from design idea to finished printed part and ensure the printed output is exactly what was intended with minimum user input.
Faster machines and ever higher printing and build volume temperatures will continue to be developed, but repeatability, reliability and quality will be key for businesses to succeed and sustain.
Continued research and development in the area of materials will increase the number of applications within the reach of FFF – softer elastomers, tougher and stronger polymers and a wider range of metals and composites.
6. What is the next step to make this sector greener?
MGC: By simplifying the process of slicing, printing and managing component data, Ultimaker continues to reduce the trial and error that is symptomatic in the FFF industry, reducing material and energy consumption. This also helps drive AM adoption, increasing the number of companies making parts on demand and in-house rather than ordering from distant manufacturers, saving transport and logistics, as well reducing lead times. Further enhancements in printing profiles and the hardware’s ease of use will continue this trend.
Ultimaker also welcomes partners to our ecosystem who drive sustainability – whether by making filament available made from recycled products, software solutions that optimize print settings in such a way that less material is used, or hardware add-ons that help to ensure first-time right prints.
7. Do you think 3D printing can take over a big chunk of part replacement market?
The need for businesses to increase the flexibility of their operations is key. During the pandemic, many turned to 3D printing technology to stay on top of their supply chains.
Static or inflexible production lines, from which companies enjoyed a stable operating environment, with returns of investment targets of more than three years things of the past. The increased volatility of the business environment has dramatically changed, forcing many companies to adopt much shorter ROI requirements.
Companies now have to ensure that their production assets and resources are flexible, and can be quickly repurposed to address market requirements or changes. Integrating technologies such as 3D printing into production and manufacturing enables greater flexibility for companies, which has been highlighted by the COVID-19 pandemic. Some interesting examples of how 3D printing has enabled companies to adapt are:
- Critical spare parts: Companies were able to print spare parts on demand, minimizing downtime and inventories, as well as ensuring business continuity
- Tools, jigs, and fixtures: These help to reduce damage, increase safety and/or enable more operating efficiencies in a production environment.
- Innovation and prototyping:3D printing allows designing, testing, embedding, and iterating in a very short period of time. This mindset also helps to quickly change production processes, when, for example, a company that normally packs shampoo bottles wants to suddenly shift to packing bottles that hold valuable vaccines, a simple 3D printed gripper can be rapidly and locally produced to ensure the changes in production lines can be made more quickly than ever before.
- Cost efficiencies: Companies with 3D printing were able to produce parts with the same functionality of those created using previous manufacturing methods, more quickly and at a fraction of the cost. Like these aluminum gripper fingers, which were converted to polymer gripper fingers, with added, replaceable hardened dowel pins.
Created by Azoth, these aluminum gripper fingers were converted to polymer gripper fingers
The above use cases highlighted by the COVID-19 pandemic clearly identify the important role that 3D Printing can and has played over the last year. Additive manufacturing will play an increasingly important role in helping companies to become more flexible and agile.
8. How has the digital manufacturing transformed this sector?
MGC: Digital Manufacturing has allowed industry to become more flexible and efficient; the rise of automation and simulation has given manufacturing engineers many tools to streamline day to day operations; Ultimaker’s Digital Factory is one such tool.
Ultimaker’s Digital Factory allows for efficient manufacturing by storing design data securely in the cloud; components can be accessed at any time and printed on demand at any location. This eliminates the need to transfer data between sites via email/usb/ftp, ensuring the latest file is always being used and prints/printers can be monitored from anywhere. The Digital Factory automatically manages the printing queue, ensuring jobs are sent to the next available printer with the correct setup. The reporting and analytics tool provides useful insights into the usage of individual printers, print fleets, projects, and applications. It’s designed to provide afull oversight of your entire 3D printing operation, while reducing costs with robust data on costs per part, material usage, and more.
Digital Factory also allows for Projects in Ultimaker Digital Factory can track the costs and print time associated with the parts as well as displaying the traditional cost and lead-time for comparison, allowing for easy make vs. buy decisions and ROI calculations.
Digital manufacturing helps accelerate the adoption of 3D printing. Detailed digital simulation, testing, and analysis of manufactured parts help ensure a part will fulfil its function the first time it is printed. It also helps define the right production method per part.
One such software solution, integrated in the Ultimaker ecosystem, is Teton Simulation – a smart slice solution that allows users to validate and optimize print parameters based on end-use requirements. Speaking generally, users will see a print time reduction of between 30-50%, and a reduction in iterations from between 5-25 to 1-2.Theseadvantages will help further accelerate both the usage of 3D printing and its environmental sustainability.
MGC: Another such example is Castor Technologies who produce software capable of analysing a company’s design data to ascertain which components would be efficient to fabricate by additive manufacturing, allowing for local manufacture when required. This helps break down barriers and speed up adoption of AM.
10. Which industry has the most demand for 3d printing during this time?
Working more efficiently and effectively is a goal of essentially every business, regardless of sector or industry. Today’s business environment makes this more challenging than ever. 3D printing is a tool for companies of all sizes that can be leveraged in warehouses, assembly lines, offices, and factories, enabling them to achieve results otherwise impossible.
Find more at https://ultimaker.com/
