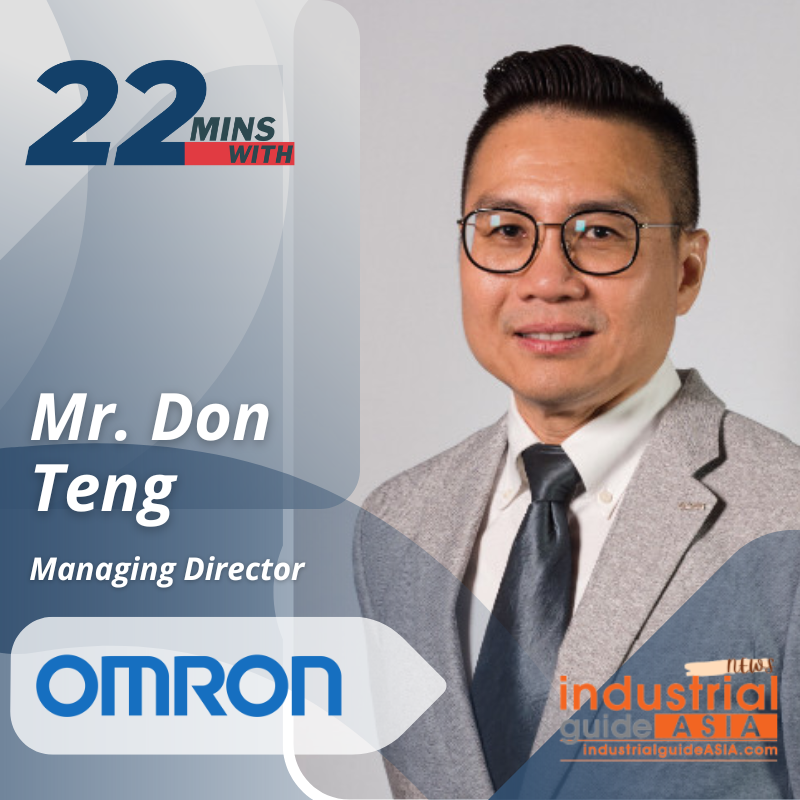
1. What are some of the key strengths of OMRON?
OMRON Automation derives its key strengths from its strong belief and commitment toward creating stronger human-machine harmony at the shop floors based on its world-renowned sensing& control technology. This is translated into our product portfolio – one of the widest end-to-end in the industry – comprising of advanced ILOR+S(Input, Logic, Output, Robotics and Safety) solutions based on our futuristic concept of innovative-Automation. It enabled us to solve manufacturers’ in numerable & diverse issues at the shop floor ranging from productivity t, speed to safety.
2. How would you implement a more structured and collaborative environment for all divisions in APAC?
I strongly believe in establishing a “happy work culture” and continuously working on improving upon it day by day. This is the first important step to ensure a more structured and collaborative work environment. A happy work culture is built upon a psychologically safe environment that enables diverse people to ask questions, raise issues, give and receive feedback, and even have differences in opinion without losing respect for each other. These are few of the simple yet effective measures towards which I am continuously working upon along with my team members to ensure a vibrant and collaborative work environment.
3. What kind of frustration did you experience in your previous experiences that can be translated effectively into a new way of thinking?
We are in the domain resolving manufacturing issues through automation technology and experience were accumulated via learning, sharing, brainstorming, and collaborating, which luckily did not lead to much frustration. So, my main take-away in previous experiences is if all of us could recognize the issue boldly and identify its root cause, it can be resolved logically. Moving forward towards our vision without past burdens is something that I would like to propagate amongst my team members.
4. What are the main features of OMRON innovative long-term strategy plan?
OMRON’s recently announced long term vision – Shaping the Future 2030 (SF 2030) focuses on three social issues and needs: Climate change, the aging of society, and increasing wealth gap among individuals.
The goals for these three issues are achieving carbon neutrality, implementing a digital society, and extending healthy life expectancy.
We believe that a society in which these issues are resolved is an ideal society where people can live an enriched life in balance with their environment.
OMRON’s industrial automation business aims to contribute towards these social needs by improving manufacturing that helps in creating a sustainable society. It aims to enrich the future for people, industries, and the globe through “Innovative-Automation”. We believe that with our unique automation capabilities based on human-machine harmony, we will be able to contribute towards creation of sustainable and innovative factories coexisting with the environment and well being of people across APAC.
5. What are the most urgent skills issues that need to be tackled in today’s supply chain industry?
The industry is witnessing an acceleration of adoption of automation in the post-COVID world. However, it is also grappling with a shortage of warehouse resources and skilled labour that is impacting its growth. This shortage of resources and skilled labour varies from country to country. Most of the APAC markets are non-homogeneous in terms of the level of automation needs; their knowledge and maturity levels are also diverse.
The level of adoption of industrial automation is far from being consistent, giving rise to multifarious, unique, and complicated skills-related business challenges. For instance, in some emerging countries, we must cater to the needs of basic digitization to capture real data.
This is necessary to understand the needs and optimization levels before moving into full-fledged solutions. While in developed countries that have embraced innovation, we need to convince the stakeholders to balance between ROI (return-on-investment) and innovation to make life better for workers. These countries are higher up the automation curve and their end-customers are more open and willing to take automation to the next level, for example applications like having platforms to track productivity in each workflow and operation, as well as having robots travelling into elevators for multi-level operations, etc.
6. How do you see robotics and automation enhancing the future of supply chain design?
Looking at the future, I believe the supply chain industry, especially intra logistics, is expected to move towards unleashing the power of data and analytics to identify gaps and bottlenecks in warehouse operations. Most organisations are keen to pursue it actively to seek improvement in productivity and efficiency.
This can only be made possible with the deployment of robotics & AI solutions ranging from Warehouse Management Systems (WMS) integration (perhaps through cloud) to multiple modes of material transfer (both horizontal and vertical), automated cross-docks, picking, sorting, packaging, etc.
Increased usage of smart3D vision, as well as deeper exploration into assets traceability using GPS/5G both within and outside the warehouse is also on the cards, which will be led by robotics and automation solutions.
7. What are the keys challenges ahead as we move to more sustainable design practices?
From replacement to collaboration, the manufacturing world has been witnessing a significant transition in the human-machine relationship over the last few decades. One of the primary characteristics of this evolution is the merging of boundaries between factories and society — necessitating transition from collaboration to “harmony between people and machines” in the manufacturing sector.
With climate change and the unprecedented situation from COVID, consumption orientation is getting replaced with sustenance orientation. The makers are now pondering over social needs more than ever, rather than only industry- and production-based needs. All this, in turn, is demanding data efficiency driven systems to do more by transitioning to knowledge-driven systems, thus delivering more sustainable results and sustainable entities.
Keeping in view the this transition towards sustainability, OMRON has outlined its direction as “Empowering People Through Automation” for its next long-term vision: “Shaping the Future 2030” (SF 2030). For the automation business, we will undertake deployment of the Innovative-Automation concept to bring in more technological innovation and enhance respect for the environment, because we believe both are essential for manufacturing and production sites. We feel that if we do this right, we will be able to contribute to a sustainable future based on harmony between people machines.
8. What key objectives should an organization have for their products/solutions in order for it to be deemed a success?
Streaming from OMRON’s mission “To improve lives and contribute to a better society”, I firstly feel the solutions have to answer a pertinent long-term need of the sector. And not only this, the organization also must ensure that it has a wider vision in place that outlines how solving this issue is going to create value for the society. Another important point to be considered here, in order to achieve this objective, is to ensure that the solution is end-to-end in nature, if feasible. This will add lot of value to the customer and will surely catalyse the achievement of the objective.
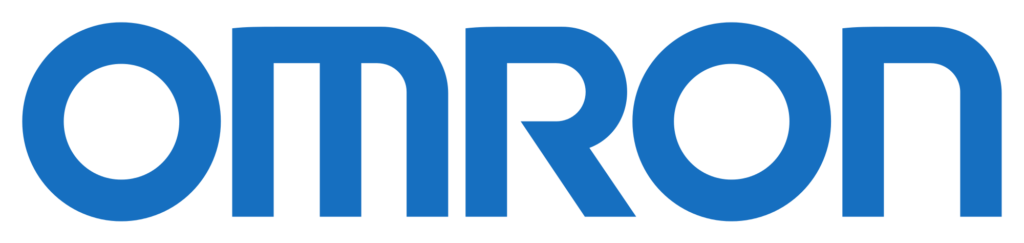