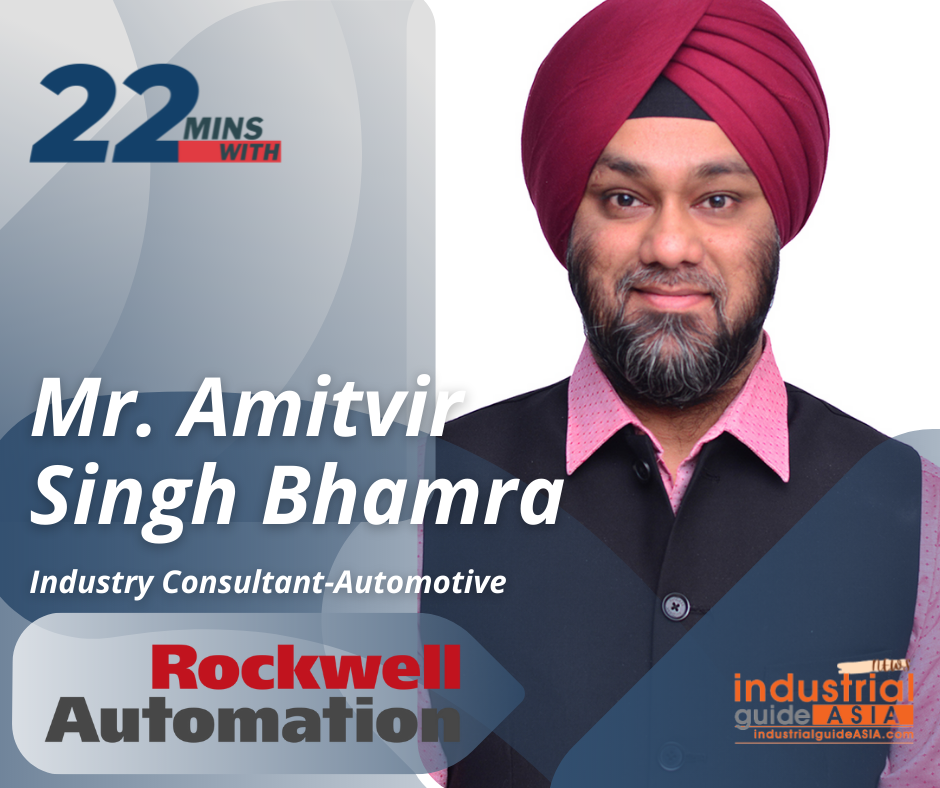
Mr. Amitvir Singh Bhamra - Industry Consultant-Automotive, Rockwell Automation
1. What were the first 5 actions you took for your department upon notice about the Covid-19 pandemic?
One of the biggest challenges brought by Covid19 was the need to work remotely and switch from in person interactions to a more hybrid or completely virtual setup. Globally, we rapidly transformed how, when, and where we worked without compromising employee safety or productivity. This included adjusting all domestic and international business travel plans due to global boarder restrictions. Rockwell Automation employs 23,500 in more than 100 countries worldwide and the safety and well-being of all our employees is our utmost priority.
As we shifted approximately 70% of our employees to work from home, we needed to ensure that telecommuting would not impact business continuity. We prioritized ensuring our employees were supported in setting up a conducive home office environment without compromising on network security by providing them with the necessary technological tools, including Wi-Fi dongles and desktop computers. Equally, we had to ensure we continued to support our customers through this time.
The nature of manufacturing meant that the immediate question most had was around how they could work with only a small number of workers physically allowed to be present on factory floors. We addressed this immediate need with advanced augmented reality (AR) tools that would help plant workers adapt to new norms and specialists respond in real time. Customer service, learning, and development did not take a backseat during the lockdowns. Employees were equipped with technology to help them remotely service customers, troubleshoot implementation issues, and continue monitoring ongoing projects through their laptops and even mobile phones, reducing their need to return to our offices.
2. There were many companies that went into limbo and were unsure about where to go next, please share with us how did your team help manufacturers in coping with their production and operation?
Rockwell Automation is dedicated to delivering the next generation of smart manufacturing and providing value for customers no matter the circumstances. When COVID-19 struck, we rose to the challenge of working hand-in-hand with customers to meet their changing business needs, whether it be expedited turnaround times, logistical shortages or accelerating productivity.
During the peak of the pandemic, when complete lockdowns were imposed by many governments, we arranged virtual technical training sessions to educate our customers on how to troubleshoot and maintain their enterprise tech tools, such as drives, servos, programmable logic controllers (PLC), and more. At the same time, our technical support teams were readily available to help address any questions or issues faced by manufacturers. We also ran complimentary e-learning courses for our customers to keep their employees up-to date with the latest developments and equip them with the skills necessary to successfully deploy the tools provided.
To help manufacturers prepare for the gradual economic reopening, we developed a start-up readiness guide to help our customers adjust and thrive in the new normal without compromising output quality and workers’ safety. This readiness guide provides a step-by-step walkthrough best practices to help manufacturers restart operations, as well as sharing scenario mapping for enhanced preparedness. Topics covered in the guide include guidance on safety checks, inventory mapping and management, test driving dormant equipment, re-establishing communications protocols, and more.
3. Has system integration becomes more crucial during this time for the factory?
For years now, Rockwell Automation has been driven by a singular vision of helping our customers realise the significance of The Connected Enterprise®. In this age of technological advancement, manufacturers need to scale output, incorporate flexibility, improve holistic visibility, enhance worker productivity, and enable truly intelligent automation. The pandemic has led many industrial players to realise they need to ramp up their ability to adapt to remote working and decentralised operations.
The Connected Enterprise® makes this possible by converging plant-level and enterprise networks to securely connect people, processes, and technologies. Better systems integration also calls for the need for bettercy bersecurity to protect an organization’s physical, intellectual, and digital assets. We work with both our customers’ IT and operations teams to establish multiple layers of protection through a combination of physical, electronic, and procedural safeguards. When developing a control system, our core security principles can be summarised in five points:
•Secure network infrastructure A resilient network security system that uses cloud technology, data analytics, and mobility tools to optimise systems monitoring
•Authentication and policy management Minimizing threats from internal resources through enabling centralised control over user access while allowing for flexibility for remote work.
• Content protection Safe guarding sensitive information such as intellectual property while maintaining productivity and quality.
• Tamper detection Having as trong coordinated response in place to detect and disable any unwanted activity, including regular backups of digital assets and the meticulous monitoring of actions an inventory.
• Robustness Connecting the enterprise under a Converged Plantwide Ethernet (CPwE), a single system architecture that allows for centralised monitoring and reporting.
4. Which sector in manufacturing recovers the quickest during this time?
Essential businesses such as F&B or pharmaceuticals are likely to recover a lot faster than say, aviation. But more importantly, it’s manufacturers who are agile and quick to pivot, that are most likely to bounce back even stronger after a crisis. Regardless of the industry or sector, digital transformation is the true key to recovering and maintaining operations and is what will allow manufacturers to adapt to new ways of working whilst capitalising on growth opportunities. A more interconnected enterprise means better data and analytics, which can improve predictability, adaptability, and long-term decision-making.
5. What challenges do your team face, especially traveling is so difficult during this time, and how are you able to diagnose cases for your clients?
Many of our customers have been classified as essential businesses. For industries such as pharmaceutical or medical equipment manufacturing, our customers have to balance meeting skyrocketing demand whilst staying compliant with social distancing measures and limits to maximum group capacity. One way we’ve managed to continue servicing customers without interruption is by providing complimentary access to our AR program; an advanced simulation tool that can capture manual activities in real-time and enable rapid knowledge transfer, bridging expertise gaps. AR allows remote experts to help onsite personnel perform critical tasks and maintenance, such as those required to recover from unplanned downtime or outages.
For example, equipment manufacturer intelligence can be streamed directly to an engineer’s device, even as maintenance staff at other plants help with the diagnosis. Mixed reality devices also help frontline employees to safely assemble complex products, by equipping them with real-time production data and instructions as required while performing the task. Simulation tools enable engineers with tasks such as mapping equipment layouts and studying the impact layout changes have on productivity and throughput equipment from anywhere in the world.
6. What do you foresee will be the next industrial trend?
Smart manufacturing is the true gateway to a comprehensive digital transformation. Seamless connectivity is the key here – integrating smart devices will spur better collaboration while data and analytics tools will enable better and faster decision making. The rapid evolution of technology in industrial automation systems requires tighter integration between devices on the plant floor and the rest of the enterprise.
This integration requires a secure network infrastructure, smart devices for efficient data collection, and the ability to turn data into actionable information. This integration of control and information across the enterprise enables industrial players to optimize their operations. To summarise, smart manufacturing can be defined as the seamless integration of control and information across the enterprise. The Connected Enterprise® will allow manufacturers to become more flexible, resilient, and better positioned for future growth, by connecting factory floors, facilities, business operations, and the people who run them.
Find more at https://www.rockwellautomation.com/en-us.html
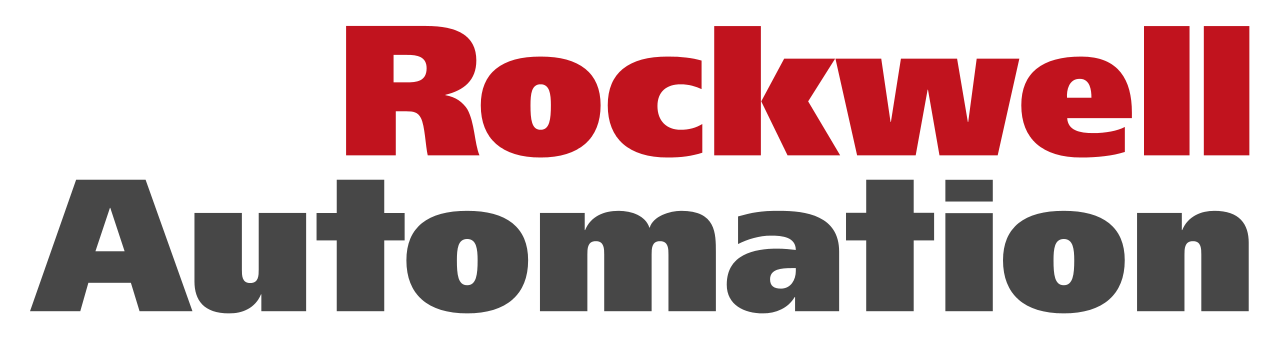