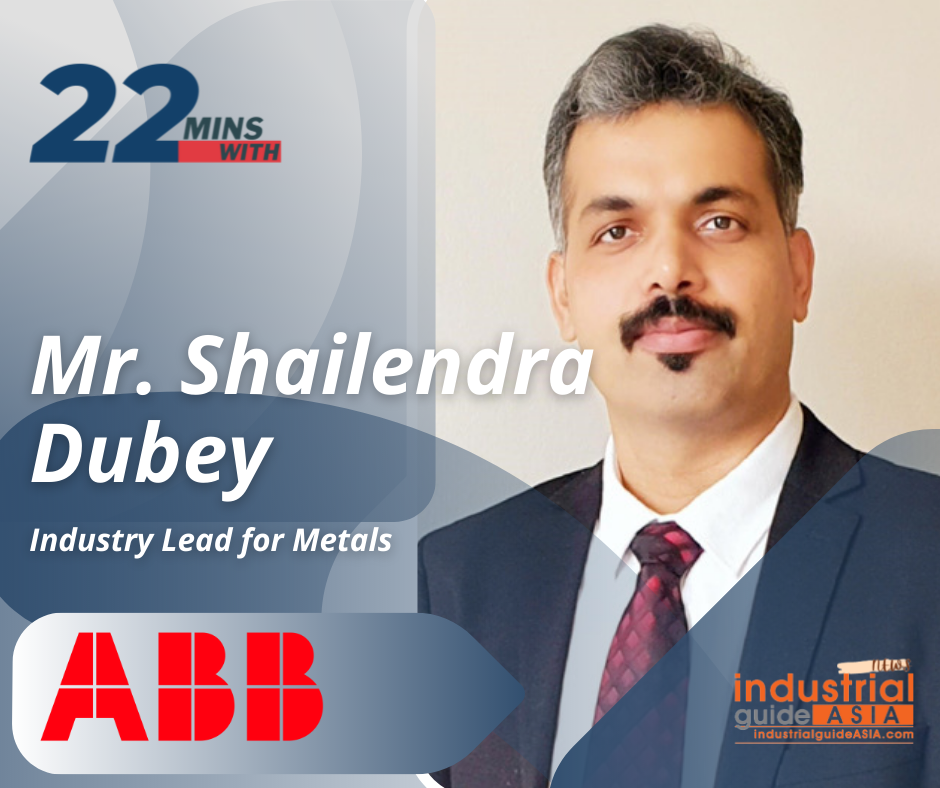
Shailendra Dubey - Industry Lead for Metals
Mr. Shailendra Dubey is Industry Lead for ABB metals business in South Asia, Middle East and Africa (SAMA) and has more than 15 years of industry experience. He joined ABB in 2006 in India and later moved to Malaysia. In 2014 he took responsibility of the metals and mining business for the South Asia hub, based in Singapore. He is an electrical engineering graduate and prior to ABB, worked with SMS Demag (SMS group) in electrics and automation. Shailendra is known for building sustainable customer relationships by anticipating and mapping customer needs, with focus on consultative sales and solutions development. He has worked in process applications such as cold rolling mills, profile mills and iron and steel making, delivering electrification, drives, motors, and automation system solutions. His focus and specialist knowledge of this market resulted in the achievement of several large strategic awards whilst simultaneously increasing the footprint of ABB throughout the metals industry in this key region.
1. What are the challenges facing the metals industry during this pandemic?
The pandemic is reshaping how companies operate across most industries. We are supporting our customers through these changes with safety the highest priority, relying more than ever on virtual communications tools and offering remote services. Globally, the pandemic has also impacted the consumption of metals. For example, we know our customers are facing substantially reduced demand for steel products.
2. This trade requires you to be on site for your clients frequently. How do you manage this during this time?
We continue to visit our customers when it is required, leveraging our network of local ABB teams to provide direct support, diligently following ABB health and safety protocols and those of our customers. Evidently, cross-border travel has been reduced within countries and between countries, so we have adapted. Particularly for our customers in other countries, we have adopted new tools to connect sites and perform necessary tasks, including commissioning.
3. What technology has your company adopted to facilitate work between you and the end users?
We have used various digital tools to connect with our customers, including video calls and file sharing platforms, which we have all become more familiar with over the last year. There is mutual understanding, with customers more open to using these tools to carry out as much work as possible remotely to ensure the safety of all teams. On top of the common tools, we are working more with Augmented Reality (AR) and other digital applications to support our customers with issues, repairs and commissioning of new projects.
4. What do you view as the most important metals issue facing our industry today?
From a global point of view, supply is currently higher than demand with an overcapacity of steel. This is undoubtedly affecting prices and the growth of the industry. It is important that businesses improve the efficiency of their operations to stay competitive and ABB is leading the way in this space as always. However, sustainability cannot take a backseat and business owners remain open to exploring tools and solutions. Many existing solutions are helping to improve productivity while reducing environmental impact.
5. How is ABB overcoming some of the known hazards within the metals industry?
Many of our digital tools help customers to remove workers from hazardous areas or shorten the time that they need to be there. Our metallurgical offerings not only improve efficiency and quality but provide for a smoother, more repeatable process with less manual intervention, contributing to the safety of workers.
Using our understanding of the metals process, we have designed digital tools to perform specific tasks. For example, we use ABB Ability™ Remote Insights to connect field personnel to ABB experts directly. The application helps us to see whatever the plant operator is seeing and utilizes augmented reality and live on-screen annotations to help the customer resolve issues more quickly. Our ABB Ability™ Performance Optimization for steel melt shop solution improves human safety by reducing exposure to hazardous hot metal zones and allowing for decision-making based on information dashboards.
6. What is a new trend in the metals industries this year?
We see a plethora of technology to assist steelmakers in their roles such as fully and semi-autonomous robots, drones, increased use of artificial intelligence (AI), virtual, augmented, and mixed reality, digital twins and ever more innovative ways to transform. Steel players around the globe are increasingly focusing on decarbonization. Overcoming the challenges to decarbonize the steel industry is one of many key steps in reaching the world’s global climate targets. Through innovation, low-carbon technology deployment and resource efficiency, iron and steel producers can reduce energy consumption and greenhouse gas emissions and enhance their competitiveness.
7. What is your strategy this year for the metals industry in Asia?
Due to global competition, metals manufacturers are under constant pressure to find new and improved ways to enhance operations and reduce costs. More powerful tools are needed to monitor operations, identify and diagnose current problems, and predict new ones before they cause bottlenecks, unplanned downtime or unnecessary use of resources such as utilities, energy and assets.
ABB’s focus is on digital solutions that combine real time, remote expert insights with continuous monitoring and process-specific data analytics. These solutions offer steel, aluminum and other metals manufacturers opportunities to reach new levels of operational performance through technology, boosting their processes and profitability. ABB will work alongside customers with the vision of continuing to transform the metals industry.
8. This pandemic has helped to speed up the whole Industry 4.0 trend. How has it been for the metals industry in Asia so far?
Industry 4.0 technologies were already transforming manufacturers’ operations before the pandemic. But the pandemic has fueled and expediated the adoption of digital technologies by a few years and the changes are here to stay. In the metals industry, the response is mixed; large steel players had already started scaling up and are now ramping up at a higher pace, the smaller players need to catch up soon to stay in the game.
9. How long do you think it will take for metals companies to transit deeper digitally?
The metals industry has a history of long lead times when it comes to adopting new technologies. While the industry has made significant investments in process control and automation, it has lagged in digitalization. However, this pace has picked up over the last few years and now accelerated by a global pandemic, the industry is all set to witness a big change in the operations and adoption of digital technologies. With the metals manufacturing companies now leveraging value out of latest technologies like data analytics and AI, the industry is racing towards a digital future.
10. Tell us how does ABB intends to transform the metals industry?
We are now in the century defined by Industry 4.0, which is progressively evolving to meet the needs of rapid and productive operations. Metals companies cannot rely on aging systems to support the business activities of the future. To remain competitive, they need to transform, create new operating and business models, and foster a digital culture.
ABB can envision, create and manage the digitalization initiatives of our customers, capture real value from Internet of Things (IoT) applications with our deep domain knowledge of the steel industry, copper, aluminum, other metals and metallurgy. Our vision of an intelligent metals plant is where ABB enable send-to-end visibility and optimization, consolidates data in a unified digital ecosystem to create impact on every aspect of operations and makes the transformation to intelligent plants a reality.
11. What is the latest technology from ABB for the metals industry?
As a technology leader ABB has always innovated, working closely with customers to directly understand the emerging trends and issues. We offer a host of customizable solutions already deployed at plants around the globe - to better monitor, control and optimize the complete value chain. Some of our new offerings like ABB Ability™ Performance Optimization for steel melt shop help boost overall productivity, safety and energy efficiency in steel manufacturing.
Our ABB Ability™ Data Analytics platform for metals offers plant-wide and enterprise-wide data integration, monitoring ,data analytics and optimization in iron, steel and other metals manufacturing -with one single platform. At ABB we believe a more collaborative approach is the way forward to implement proactive maintenance strategy tailored to the needs of your metals plant - improving availability, reliability and reducing maintenance costs.
Find more at https://global.abb/group/en
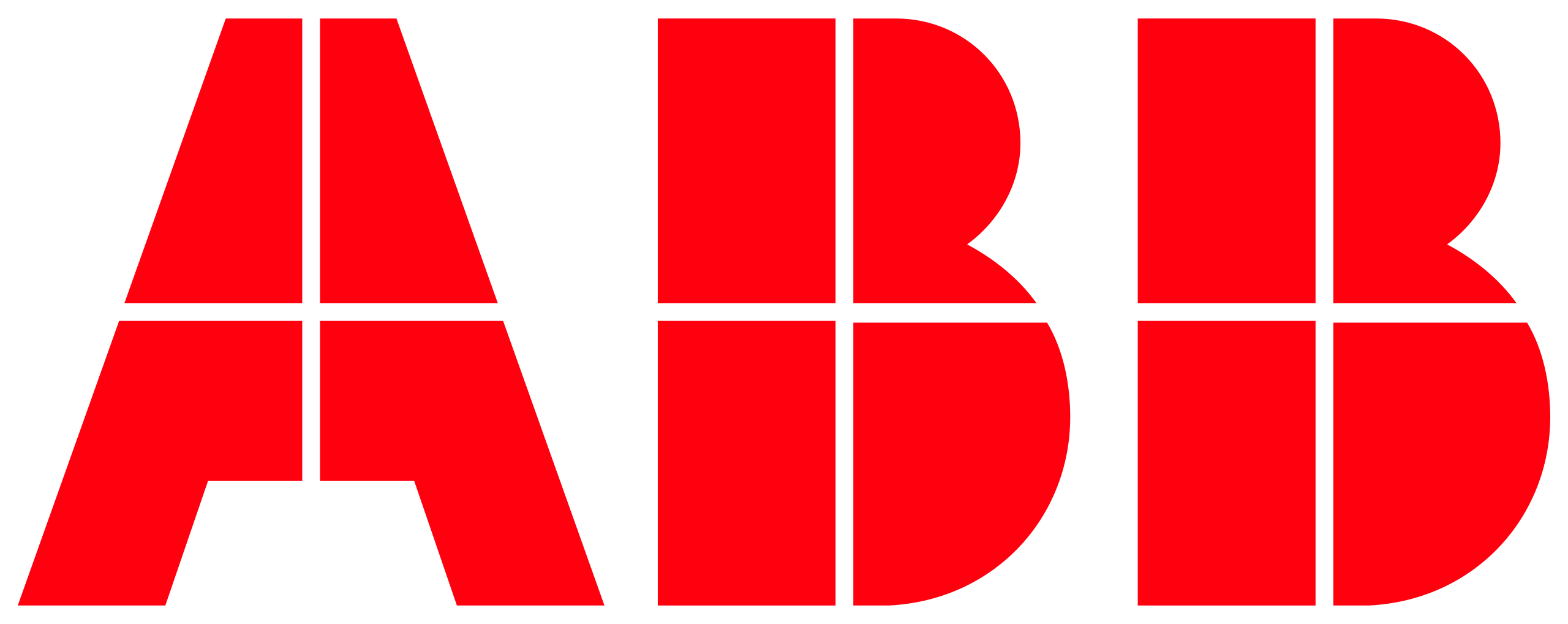