Honeywell today announced that China Tianying Inc. (“CNTY”) will apply Honeywell’s UpCycle Process Technology in their planned plastics recycling factory in Jiangsu Province. The facility will convert mixed waste plastics into recycled polymer feedstock (RPF), enabling the development of a circular economy for plastics. It will become the first commercialized waste plastics recycling facility using Honeywell’s UpCycle Process Technology in China.
The plant will be able to convert mixed waste plastics into recycled polymer feedstock utilizing Honeywell’s UpCycle Process Technology. Honeywell UOP will provide related engineering work and technical services for the project up to its startup and commissioning, and provide technical support services for the plant's operation, optimization, monitoring, and maintenance during its lifetime.
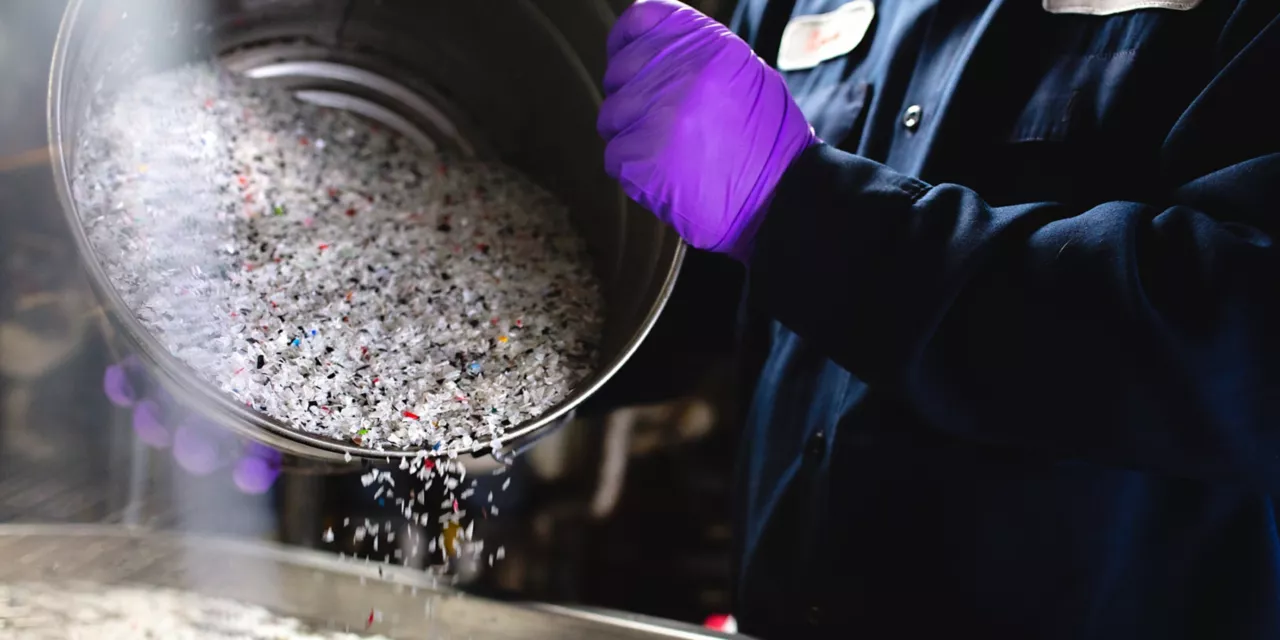
This project ushers in collaboration between Honeywell and CNTY on advanced plastics recycling, as well as the first application of Honeywell’s UpCycle Process Technology in China. In light of the success of the first facility, CNTY intends to apply Honeywell UpCycle Process Technology in building more waste plastics recycling plants in the future. The two parties will also explore potential collaboration in various fields, including waste plastics pre-treatment and pyrolysis equipment manufacturing.
“Honeywell’s UpCycle Process Technology not only expands the types of recyclable plastics that helps close the loop within the plastics supply chain, but also helps minimize consumption of fossil fuels over the course of virgin plastics production, reducing the carbon footprint,” said Vimal Kapur, president and CEO of Honeywell Performance Materials and Technologies. “We are glad to collaborate with CNTY on commercializing this innovative technology in China. Its application addresses challenges posed by waste plastics and promotes a circular economy in China and the world, enabling a more sustainable future of plastics industry.”
Honeywell’s UpCycle Process Technology is a ready-now technology that utilizes industry-leading molecular conversion, pyrolysis, and contaminants management technology to convert waste plastic back to Honeywell Recycled Polymer Feedstock, which is then used to create new plastics. The UpCycle Process technology expands the types of plastics that can be recycled to include waste plastic that would otherwise go unrecycled, including colored, flexible, multilayered packaging and polystyrene. When used in conjunction with other chemical and mechanical recycling processes, along with improvements to collection and sorting, Honeywell’s UpCycle Process Technology has the potential to increase the amount of global plastic waste that can be recycled to 90%1,2. This would represent a considerable increase in the amount of waste plastics that can be turned into polymer feedstock.
“We look forward to working with Honeywell on establishing a benchmark project in resource recycling. By jointly tapping into the technological and social values of such a project, we will promote green development and improve the quality of the environment where we live,” said Yan Shengjun, Chairman of CNTY. “CNTY taps into its diverse experiences in superior environmental management along with Honeywell’s ground-breaking technology for waste plastics recycling, enabling us to play a leading role in promoting resource recycling.”
CNTY is a listed company with international presence. It is engaged in zero-carbon clean energy technologies, smart urban environmental services, and resource recycling and recovery. Its businesses extend from smart urban environmental services, waste-to-energy power generation, renewable energy power generation, regional energy centers, hydrogen energy centers, and the investment, construction, and operation of circular economy industrial parks, to the reduction, recycling, and harmless treatment of kitchen waste, hazardous waste, and construction and demolition waste, as well as the research, development, and manufacturing of environmental protection equipment and energy storage systems.
Honeywell committed to achieving carbon neutrality in its operations and facilities by 2035. This commitment builds on the company’s track record of sharply reducing the greenhouse gas intensity of its operations and facilities as well as its decades-long history of innovation to help its customers meet their environmental and social goals. About 60 percent of Honeywell’s new product introduction research and development investment is directed toward products that improve environmental and social outcomes for customers.
Assuming sorting and collection improves to recover most waste plastic, and chemical recycling, including Honeywell UOP UpCycle Process, is widely deployed. The 90 percent of waste plastics that could be recycled may change depending on the number of consumers or communities that have access to recycle waste plastics or the availability of recycle facilities.
Honeywell UOP analysis of US EPA Advancing Sustainable Materials Management: Facts and Figures 2018 and IHSMarkit 2019 world polymer consumption data.