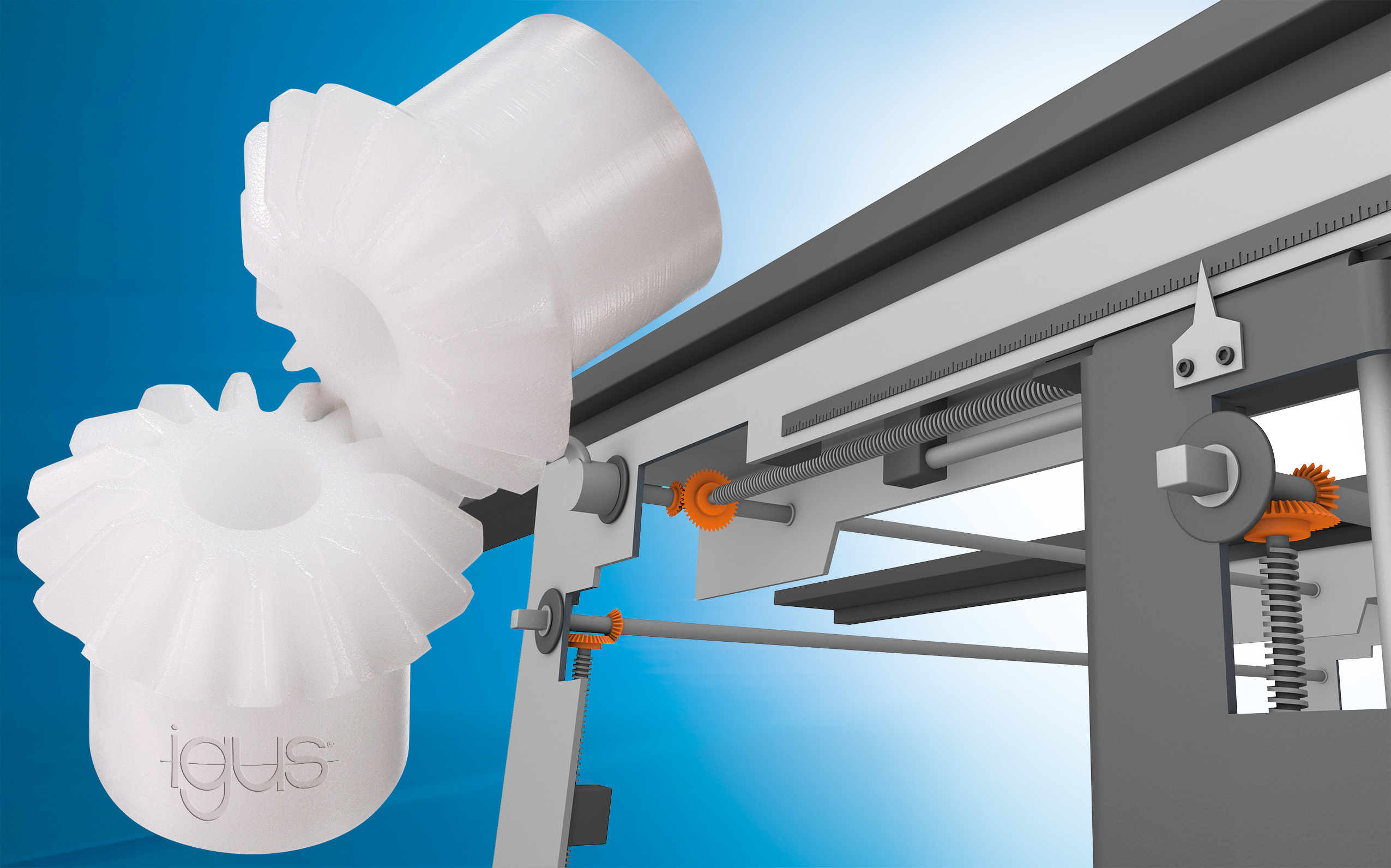
Bevel gears made of high-performance plastics as a cost-effective and maintenance-free alternative to metallic solutions
Bevel gears are suitable as drive elements in order to be able to transmit forces at a 90 degree angle. Especially for simple tasks, igus has now developed bevel gears made of two abrasion-resistant, durable high-performance plastics. They are not only lightweight and cost-effective, but also completely free of external lubrication. This reduces the time and cost of maintenance.
Gears are widely used as drive elements: in clockworks, in e-bike drives as well as actuators and locking systems. However, if forces have to be transmitted around corners, bevel gears are the means of choice. They can undertake format adjustments in the food industry, for example, via a 90-degree angle, eject packages in logistics and make assembly lines in resource supply departments and automotive industries flexible and quickly adaptable. igus has developed bevel gears made of two high-performance plastics especially for use with low and medium loads.
"With iguform S270 and igutek P360, we have two materials in our range that have already proven themselves in the field of gears and are also ideal for use as bevel gears," says Steffen Schack, Head of the Business Unit iglidur gears at igus GmbH.
iguform S270 is characterised by a low coefficient of friction as well as a low moisture absorption. Bevel gears made of igutek P360 have a very high wear resistance and toughness, which makes the drive elements insensitive to impacts. The bevel gears made of the tribologically optimised plastics are popular with users because they are cost-effective, lightweight and, unlike metal bevel gears, do not require external lubricants. This reduces maintenance intervals on machines and systems and increases hygiene and cleanliness.
Individual special series from injection moulding
"With the help of simulation tools and data from our in-house 3,800-square-metre test laboratory, we can provide customers with individual advice and support in choosing the right material and gear geometry, from prototype to series production," explains Steffen Schack. All bevel gears are available in six different transmission ratios, plus seven modules for power transmission. If the standard dimensions do not fit, igus can produce parts in-house with over 800 injection moulding machines and operates its own tool shop. "We can manufacture customer-specific special parts cost-effectively within a few weeks with the help of our new master moulding system in the field of gears," explains Steffen Schack.
ABOUT IGUS
igus GmbH develops and produces motion plastics. These lubrication-free, high-performance polymers improve technology and reduce costs wherever things move. In energy supplies, highly flexible cables, plain and linear bearings as well as lead screw technology made of tribo-polymers, igus is the worldwide market leader. The family-run company based in Cologne, Germany, is represented in 35 countries and employs 4,150 people across the globe.
In 2020, igus generated a turnover of €727 million. Research in the industry's largest test laboratories constantly yields innovations and more security for users. 234,000 articles are available from stock and the service life can be calculated online. In recent years, the company has expanded by creating internal startups, e.g. for ball bearings, robot drives, 3D printing, the RBTX platform for Lean Robotics and intelligent "smart plastics" for Industry 4.0. Among the most important environmental investments are the "chainge" programme – recycling of used e-chains - and the participation in an enterprise that produces oil from plastic waste (Plastic2Oil).