A few weeks ago we took our first look at the new multi-material jetting printer from Berlin-based 3D printing company Quantica.
The company revealed the design of its open R&D printer at Formnext 2022 in Frankfurt.
We caught up with them post-event to take a look at some of the printed samples they had on display.
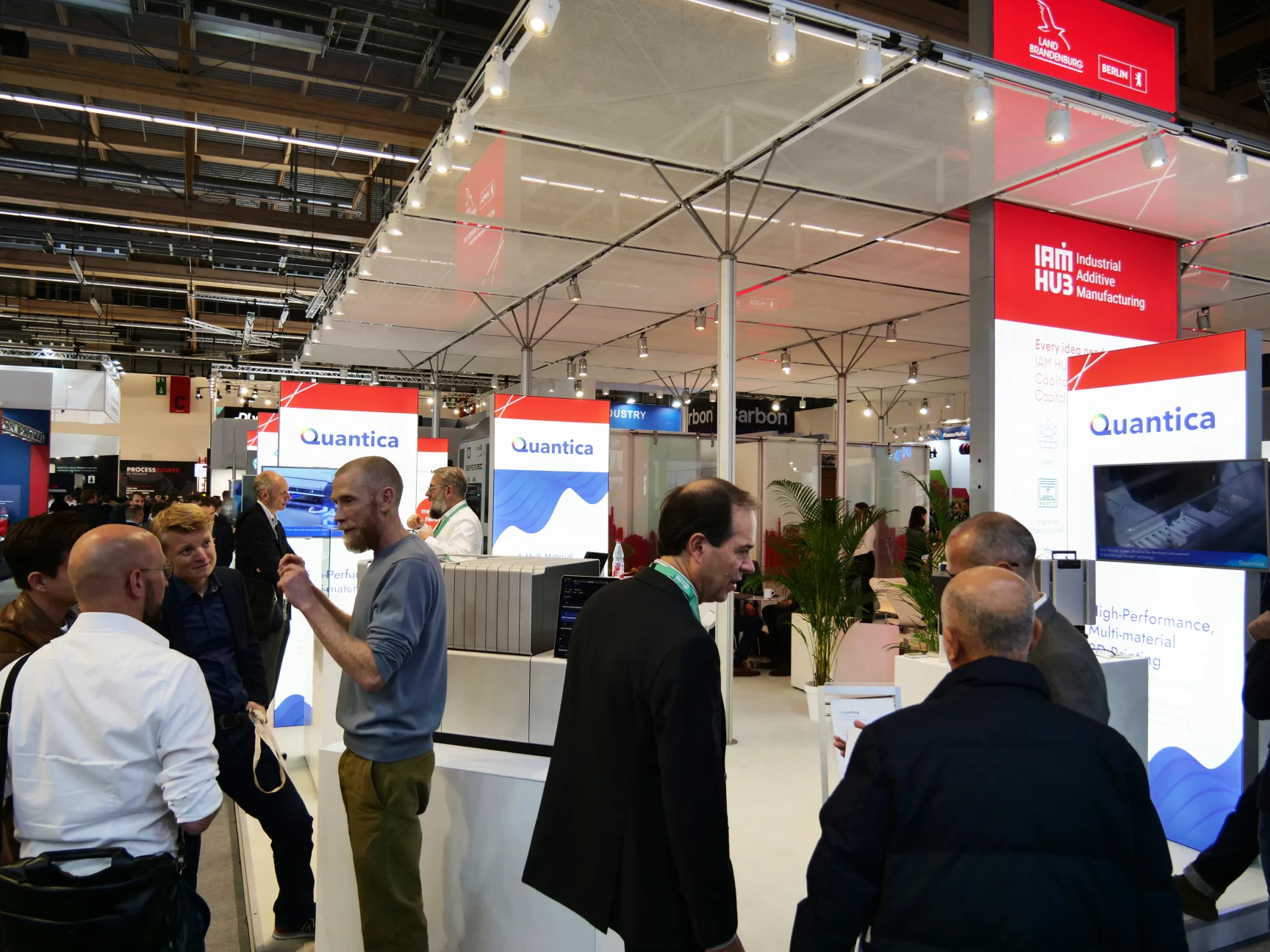
Recap
As you may recall from our previous article, Quantica’s NovoJet C-7 was developed as an open desktop system for multi-material 3D printing application development. Its full range of tunable parameters make the system perfect for those researching in the domain of new material development.
The utility of the NovoJet printhead technology lies in its ability to print materials that are 15 times more viscous than traditional inkjet printheads, together in a single process.
This opens up new possibilities for delivering high value end-part products with properties such as high toughness, temperature resistance, conductivity, biocompatibility, and flexibility manufactured in one process.
At Formnext, the team was printing with 3 different materials. However, in the final NovoJet C-7 design, the printer will be capable of printing with 7 different materials combining different colors, functions, mechanical properties, and more.
Below we will take a look at the various samples and materials that the team showcased at the expo.
Multi-Material Wristband
The first sample we will take a look at is the multi-material wristband that was printed on site at Formnext. The wristband model is made of 3 different materials that were printed together in a single process.
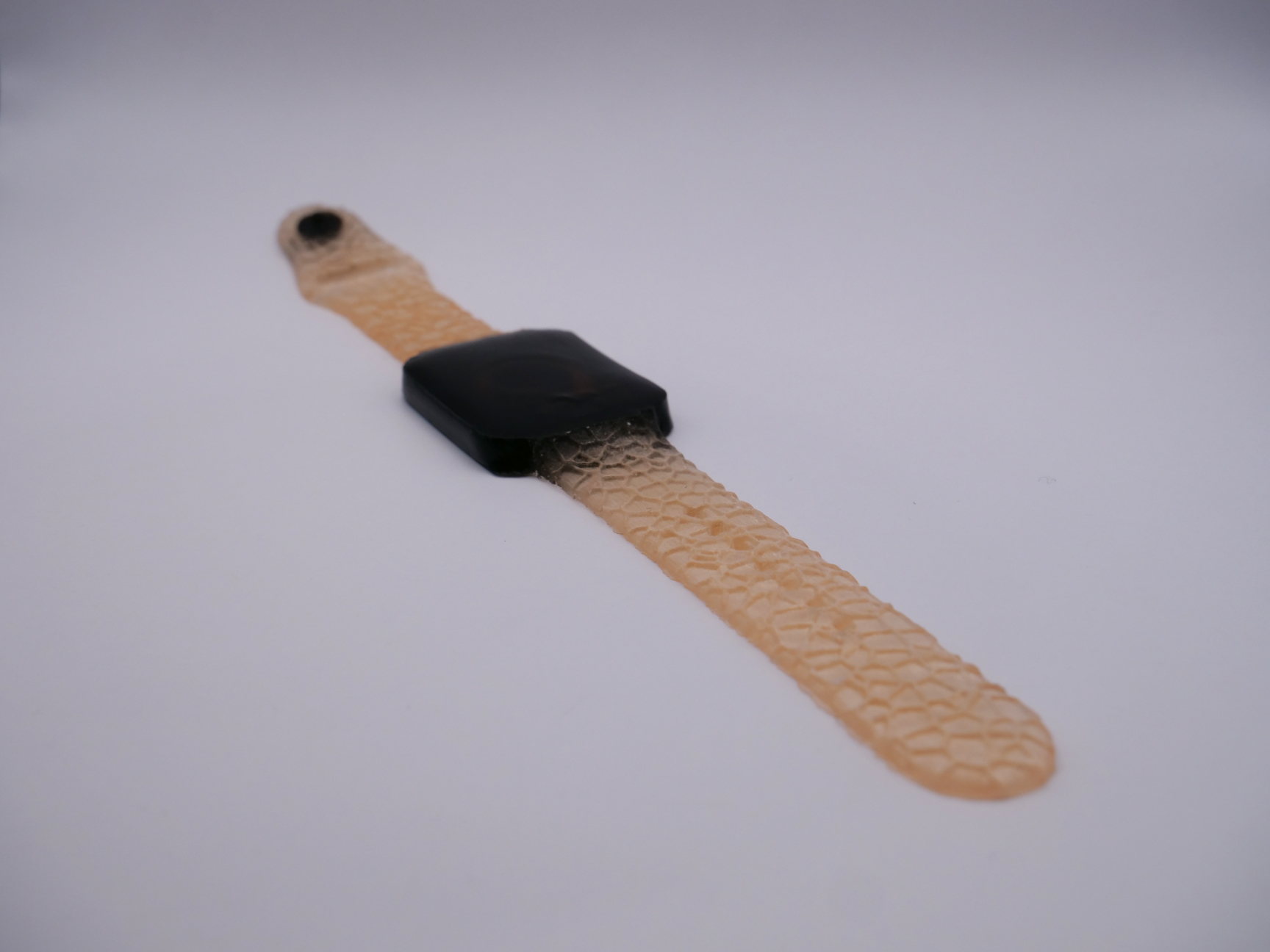
Multi-Material_Wristband
The black center component was printed with a hard biocompatible DLP/SLA resin. The semi-transparent orange straps were made from a 3D printing photopolymer designed specially for LED curing systems. A texture was added to the strap for aesthetic purposes. The strap material has improved elongation, and better resistance to breaking and tearing.
The third material used was a soluble support material, which is not shown in the picture. The soluble support material can be removed both manually, by breaking it away by hand, or by dissolving in water.
Multi-Material Denture
The denture mockup was printed to demonstrate the printing of two different materials together.
The material used to print the teeth was a creme white, opaque, methacrylate-based resin which is commonly used for orthodontic dental models.
The second material (for the gum) was a light pink, polymerizable resin which has been designed to be used in conjunction with extraoral light-curing equipment.
Both materials are used for the fabrication and repair of removable full and partial dentures, and base plates.
Denture_Model
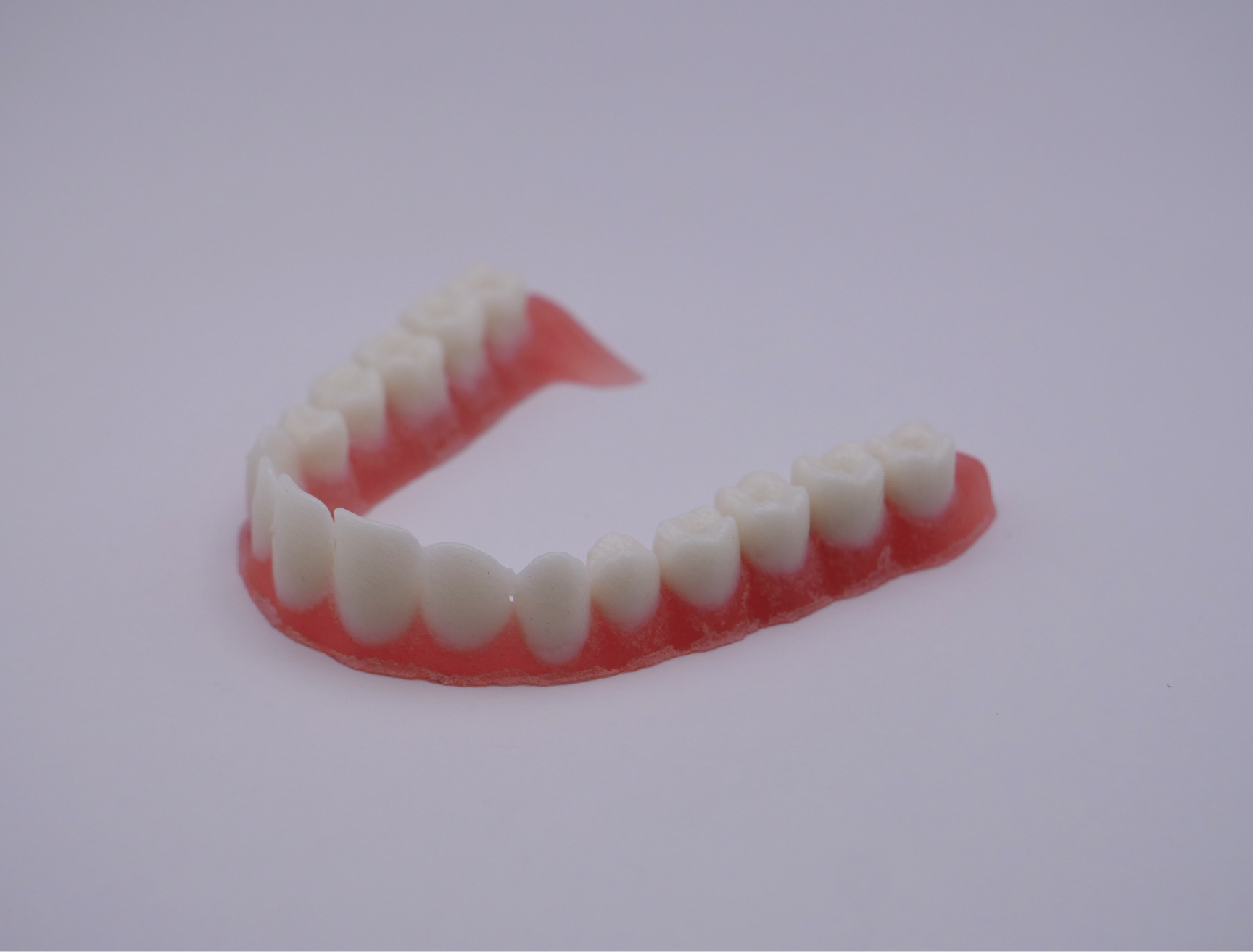
Multi-Material Finger Cross Section
This next model is a multi-material cross section of a simplified representation of a finger.
The bone part was printed using a white resin designed to be used in conjunction with extraoral light-curing equipment. This material is biocompatible and is also certified for dental additive manufacturing.
Multi-Material_Finger_Model
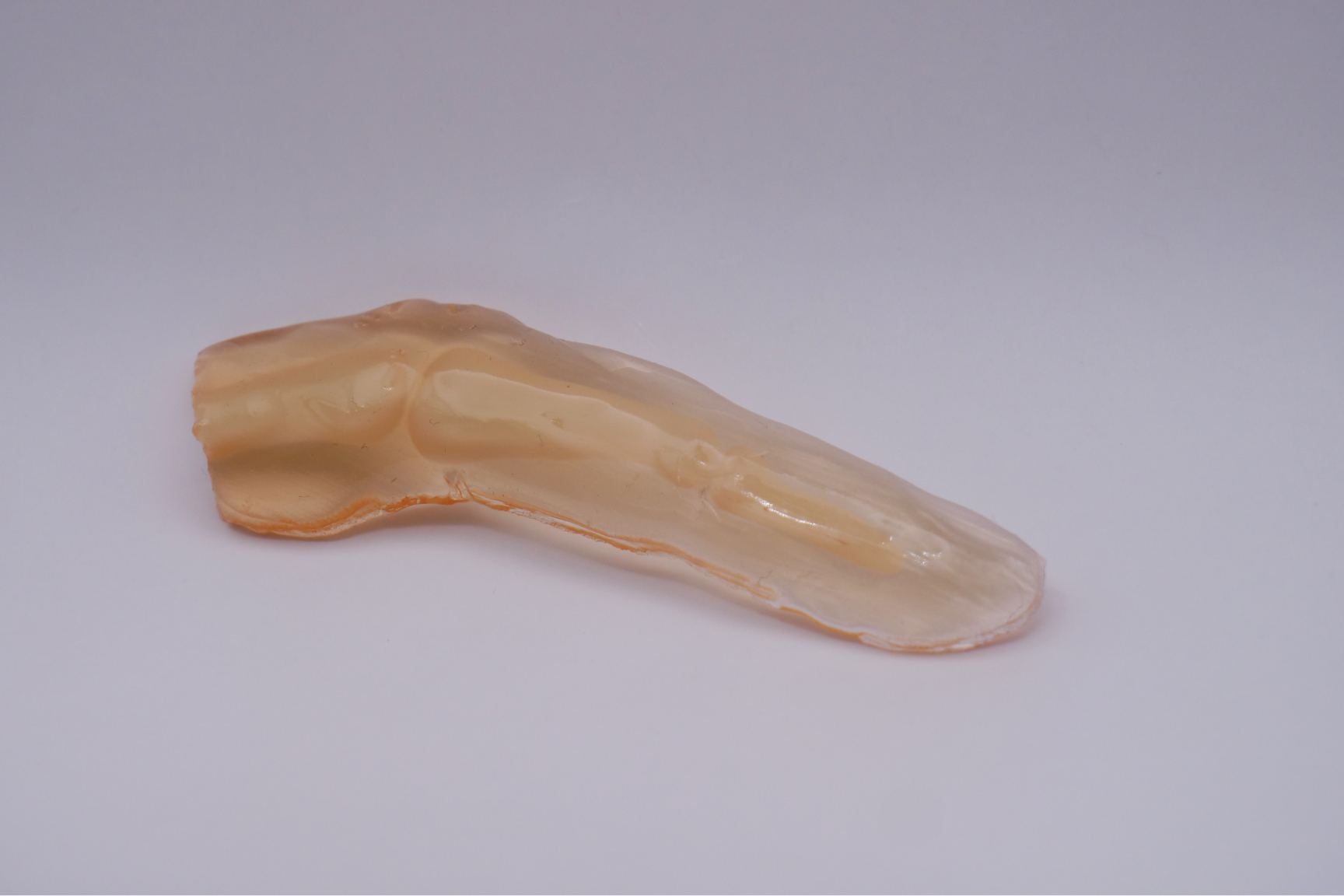
The semi-transparent part, representing the skin and muscle, was printed with a flexible photopolymer designed specially for LED curing systems. This material features improved elongation to break, and superior tear resistance.
The entire model was printed in one go, with minimal post processing.
Tough, Heat Resistant Dog Bone
Dog bones are a staple of material testing, and if you are in the materials development game, you will likely have printed some of your own already.
This specimen was printed with a black, heat resistant photoplastic resin with a HDT of over 230°C, and good dimensional stability under low loading.
This material is ideal for high temperature and low pressure environments, and is well suited for the prototyping of high temperature parts, and custom molds.
dog bone
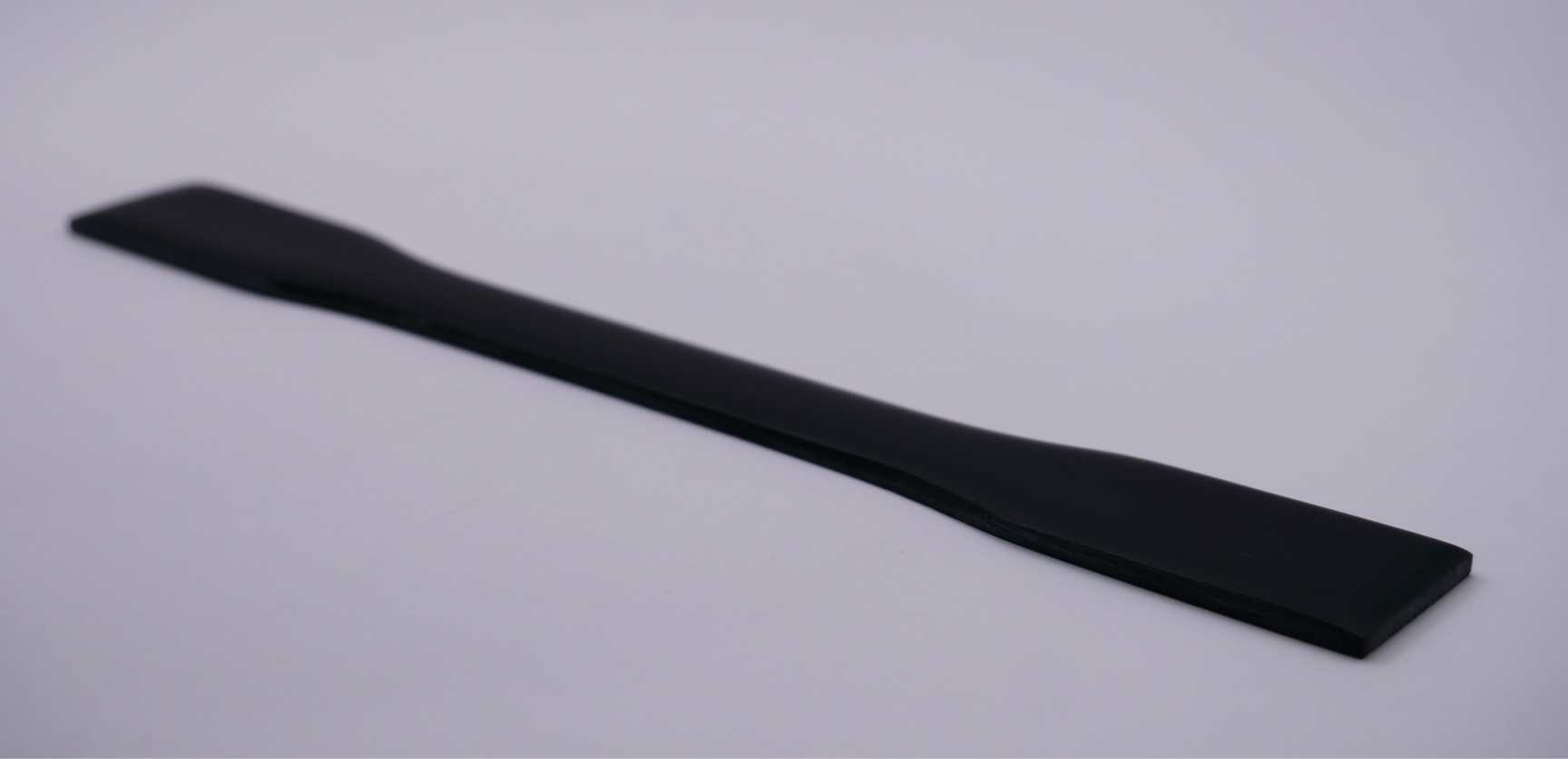
There are limited solutions for heat resistant materials in the wider field of additive manufacturing, and none available in material jetting. This sample represents a milestone for Quantica in demonstrating their ability to print more functional materials.
Heat resistant and flame retardant materials are highly valued in the rail, automotive, aerospace, and oil & gas industries.
Combined Hard and Flexible Model
This rectangular print sample showcases the ability to print two functionally different materials together on a voxel level. The sample is flexible on one end, and rigid on the other, and they blend together towards the center.
Gradient_Model
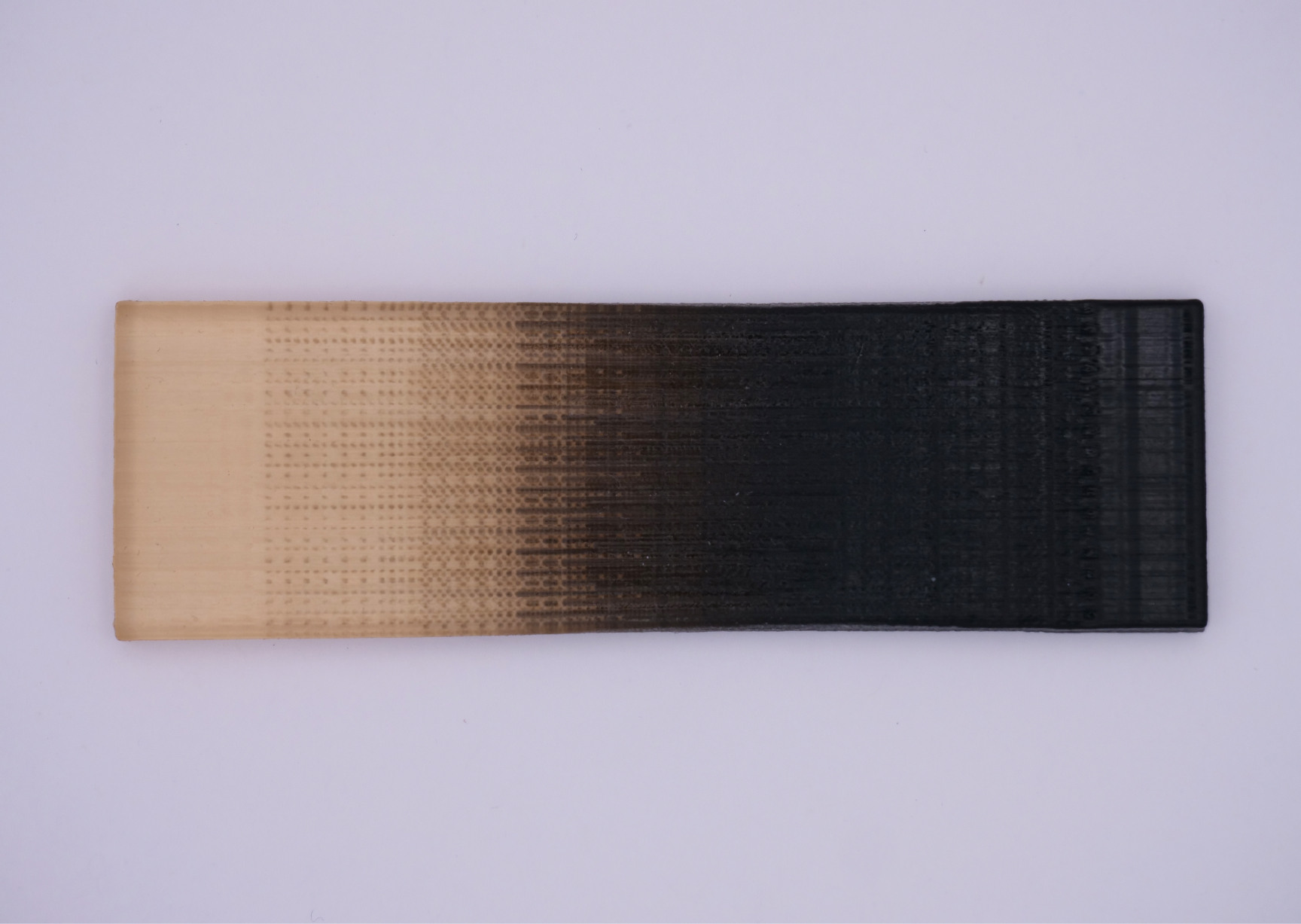
The first material is a black, biocompatible, light curable resin which can be set with light curing equipment,
The second material is a semi-transparent, flexible 3D printing photopolymer designed specially for LED curing systems. This material features improved elongation to break properties and improved resistance to tear.
Printheads
Quantica also showcased their current and next generation printheads.
The NovoJet X is Quantica’s first printhead that was designed, and was used extensively by the company for development purposes.
The most recent iteration, the NovoJet 1, is the variant that will feature on the NovoJet C-7. The NovoJet 1 features 3x as many nozzles as the development model and a recirculating flow system.
High-viscosity printhead
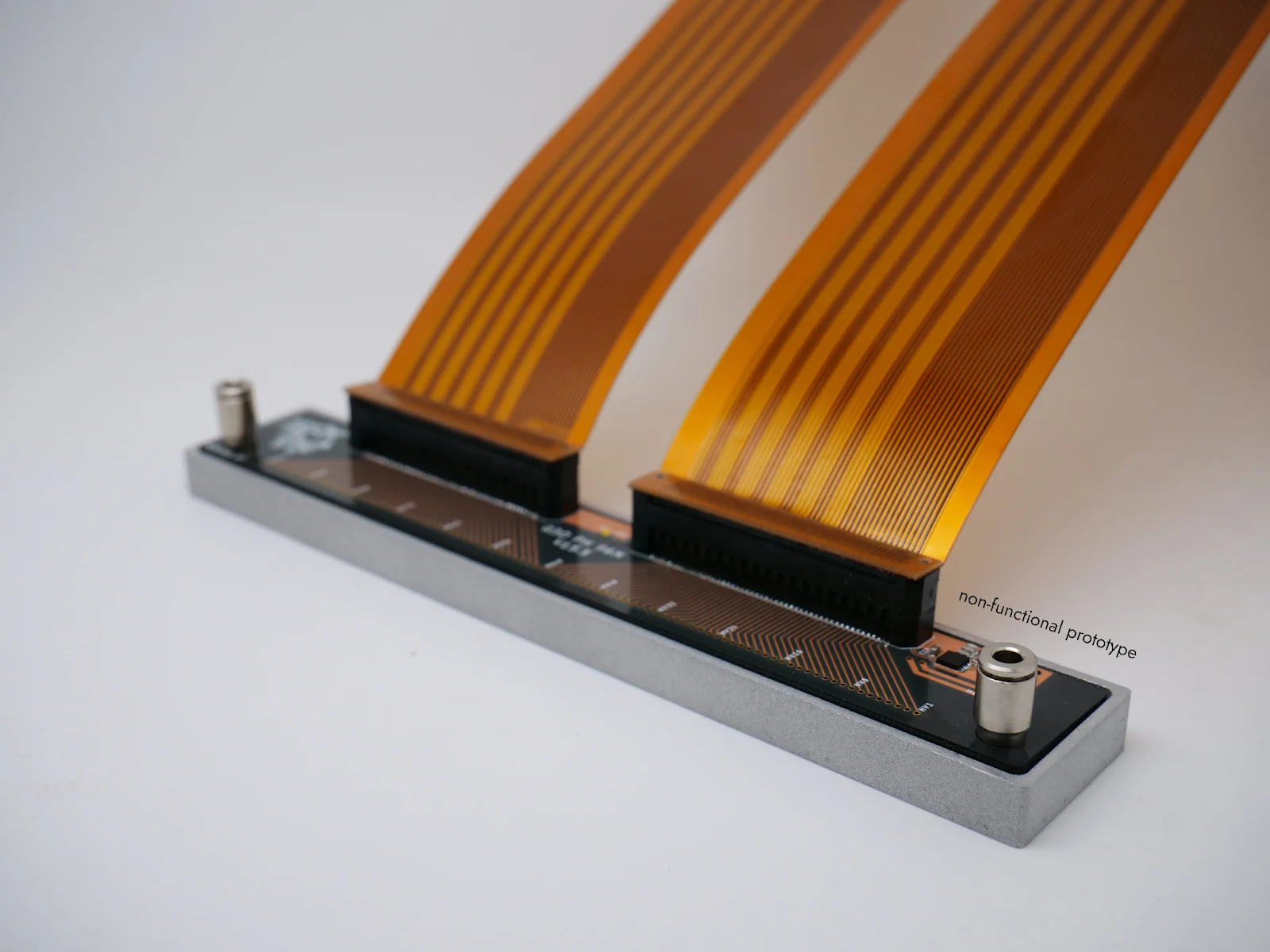
High-viscosity printhead. (Image Credit: Quantica)
Both types are capable of printing with a Fluid viscosity range (at ejection) of 1- 380mPa•s which is equal to approximately 4000mPa•s at ambient temperature.
High level specs for these include:
NovoJet X Printhead
– Nozzles: 24
– Frequency: 7-8 kHz
– Flow Type: End Firing
– Fluid viscosity range (at ejection): 1- 380mPa•s
– Temperature: 15C°-110C°
NovoJet 1 Printhead
– Nozzles: 96
– Frequency: 20+ kHz
– Flow Type: Recirculating
– Fluid viscosity range (at ejection): 1- 380mPa•s
– Temperature: 15C°-110C°
Summary
By combining different materials at the voxel level and in the same print, Quantica has opened up the ability to create new functional materials with capabilities far beyond those that can be printed with traditional resin systems.
Traditionally a lot of the materials in inkjet and other jetting technologies tend to be low quality in terms of durability, and display low resistance against warping or drying out. This is due to the need to dilute the material in order to jet it from the nozzle.
This dilution often reduces the mechanical properties of the final printed part, and this often results in prints that are less durable than a part printed with an unadulterated resin.
Quantica’s goal is not only to help those working in material development to rapidly iterate their material designing workflow, but to open up new materials in order to print better, longer lasting, end use products.
Printing materials with higher viscosity ranges means that better materials, with better material properties can now be produced. This allows manufacturers using jetting systems to move away from making short lived parts and products for prototyping, and into the domain of production grade parts.