Who would have bet that the company from whom you purchased your first desktop inkjet printer in 1998 would leverage the same technology to become a major player in the 3D printing industry?
Didier Deltort, who self-describes as “a hardcore engineer and R&D guy and technologist,” may have had an idea. He last worked for HP back when it was still called “Hewlett-Packard.” The company in 2015 split between its enterprise products and services group, renamed Hewlett Packard Enterprise, while the computer and printer businesses became HP Inc.
In 2021, HP President and CEO Enrique Lores asked Deltort to return as HP’s President of Personalization & Printing. Deltort was excited about HP’s additive journey since revealing in 2016 its first 3D printer and partnering since with companies like GM, John Deere, Schneider Electric, Siemens and Volkswagen on additive projects.
He also considers additive as disruptive technology like 5G, AI and robotics, and therefore exciting to work with, though it’s taking the technology longer than expected to hit its stride. The additive manufacturing industry hasn’t met the $50 billion size Deltort regularly saw predicted five years ago–sitting between $14 billion and $15 billion, depending on who you ask.
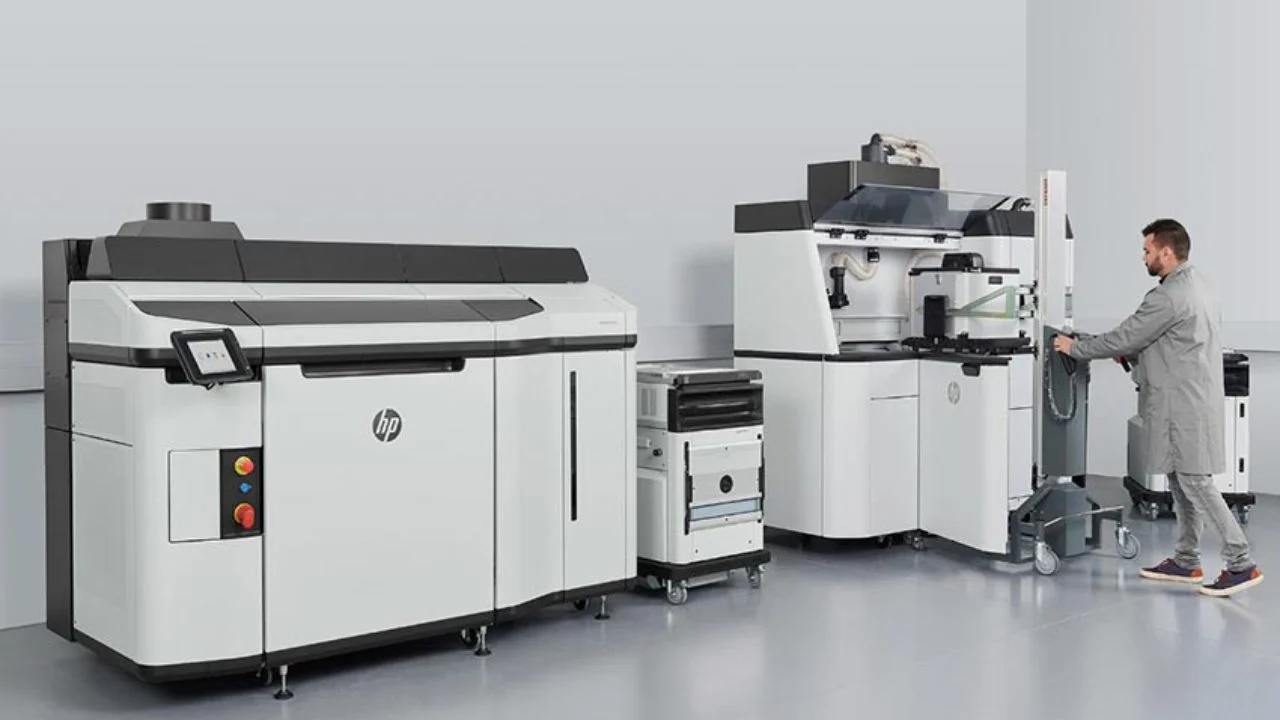
Additive’s Limits Drive New Advancements
Deltort expects it’s only a matter of when, not if, additive grows to that size once companies like HP figure out how to get around the manufacturing industry’s recurring pain points with the technology. For example, too many mechanical engineers and product designers don’t know what additive can accomplish.
“Putting in the hands of mechanical product designers the right tool so that they can pick up the right parts to be designed for additive manufacturing, that’s No. 1,” Deltort says. “No.2, it’s the breadth of materials. If you go to traditional industries and manufacturing processes like injection molding, they have thousands of materials. With additive manufacturing [we have far fewer] materials available today for the designers. That’s the second bottleneck.”
Scaling additive beyond rapid prototyping or low-volume presents a challenge because the technology lacks predictability and reliability, says Deltort.
“I want to predict what my parts will look like, what the mechanical properties will be, the finishing, and I want to make sure that I can reproduce this process millions of times,” says Deltort. “And let’s be honest. Additive manufacturing has not been the best predictable and reproducible and repeatable process in the manufacturing industry,”
Then there’s the labor concern. Additive currently resists automation.
“You go to injection molding factories, it’s fully automatic. There is almost no labor in those factories. With additive manufacturing, you need to have operators. You need to have people to pack [raw material], to unpack, to clean etc.,” Deltort says.
It’s also still too expensive to mass produce parts additively versus using traditional casting methods, Deltort adds. The laundry list of challenges explains why so few companies have scaled additive.
“There are probably less than 10 companies in the world who have really replaced traditional manufacturing technologies and processes with additive manufacturing,” Deltort says, citing the medical device and aviation industries as star players in this regard, while also recognizing the automotive industry’s gradual embrace of the technology.
The Richest Territory for Additive Growth
Addressing the pain points dictates HP's additive business strategy, and even with all its related challenges, additive still has plenty of room to grow. Deltort has his eye on some key industries to target.
“If you look at within industrials, the jigs and fixtures and so on, [there are] still some opportunities and this is for us to educate,” Deltort says. “Then, I would say within the consumer goods industry, in sports and wellness, and watches and all those things. We’ve started to work with them but could do better.”
Consumer goods companies could learn that with additive, manufacturing technology points could exist closer to customers, decreasing or even eliminating the need to ship products around the world.
The supply chain crisis presents a big opportunity. Today, companies maintain large stores of spare parts to provide immediate availability for plants. Deltort says suppliers could 3D print spares at plants, only when needed, reducing storage costs and delivery delays.
Pursuing these opportunities often depends on working with manufacturers’’ innovation centers. HP has installed its 3D printing technology and connected these centers with business units to make use cases for additive.
“We have done a fantastic job at HP at putting in almost every single service bureau and large companies’ additive manufacturing innovation center at least one of our products,” Deltort says. “But, from what I’ve seen, the communication between those innovation centers and business units is not always taking place.”
Additive-On-Demand Drives Adoption
There’s a fifth bottleneck for additive’s growth: Total cost of ownership. Industrial 3D printers cost hundreds of thousands of dollars. Smaller companies may purchase a desktop 3D printer for prototyping, but that’s all they can afford. For a medium-sized company that needs parts with complex geometries–excellent candidates for additive, but only at low volumes–investing in 3D printers might not make sense.
Service bureaus like Xometry and Fathom (that employ HP technology) have therefore become an important part of the additive ecosystem, says Deltort.
HP targeted this segment in 2016 and began making headway into the additive industry. Deltort has noticed that many large companies still favor service bureaus, even companies large enough to afford innovation centers or to purchase enough additive machines to scale in-house.
“Or, they go after contract manufacturers like Flex, GKN [or] Yazaki for the automotive industry,” Deltort says.
It’s really, in his experience, the required speed of iteration that drives companies to insource additive.
“Wallbox, an EV charger company, have been leveraging our additive manufacturing technology because the engineering team wanted to iterate. Every time they needed a mold, it had to come from Asia-Pacific. It was costing $75,000 per and required a lot of lead time,” Deltort says. Wallbox eliminated the costs and delays by embracing additive in-house.
Deltort understands that the long-term success of additive manufacturing hinges on complementing, not replacing, traditional manufacturing methods. This highlights the importance of HP’s additive education efforts, helping manufacturers lay the groundwork for successful deployment and scaling of the technology.
For instance, industrial 3D printers need a dedicated space within plants to provide the specific, optimal conditions, like temperature. Even the best printers in optimal working spaces won't provide reliable, predicable results. They need reliable operators as well, with the right training and maintenance protocols.
It also helps if plants have enthusiastic operators for the technology, thought this rarely presents a problem.
"People will buy a piece of equipment which costs between, lowest price point is probably $300,000, up to $1 million. They are enthusiastic. You don’t spend this kind of money without being enthusiastic about the technology,” says Deltort.
HP also paves the way toward new companies adopting additive by advancing the technology. In 2018, HP revealed at Dassault Systemes' Solidworks 3D conference a new, clear additive material to make the technology more precise and affordable. In 2020, HP announced the development of a new polypropylene material through partnership with chemical company BASF.
“Our strategy has been to work with the best materials companies, like BASF,” says Deltort. “We have decided not to create our own materials, but to leverage those materials from those chemical companies which have years of experience in material sciences.”
It’s a matter of incremental technology advancements and carefully uncovering the best growth opportunities, but Deltort feels the conditions for additive’s success aren’t going anywhere in the near future.
“We have made some progress. The growth is not where it should be. But, I’m sure there will be some opportunities through the ongoing world crisis around sustainability to improve and have a bigger impact with additive manufacturing.”