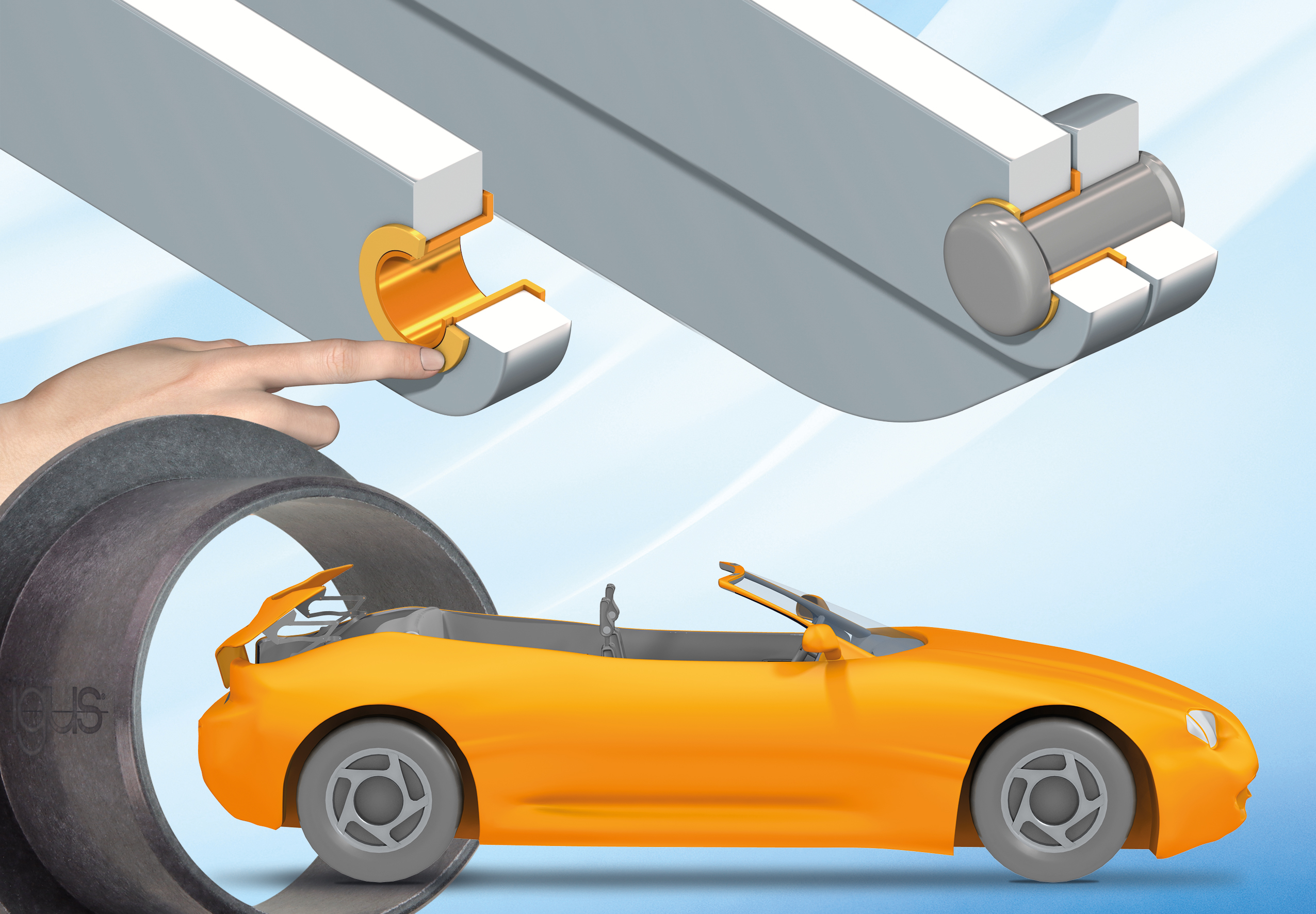
igus develops the new, highly wear-resistant iglidur F300 material for e-coated assemblies
In practice, it is not easy to cost-effectively produce clearance-free multi-link hinges for spoiler kinematics and soft-top and hinge systems. Frequently only roughly punched holes with a limited amount of fine cuts in the guides combined with cold extrusion rivets require costly bearing recalibration. With its plain bearings made of tribologically optimised plastics, such as the new electrically conductive iglidur F300 material, igus offers a technically better solution that costs less. In the e-coating process, the bearing recalibrates itself and also prevents corrosion.
Wind, sunshine and a lonely winding road. This is how you imagine a relaxed ride in a convertible. But in wind, rain and city traffic, the driver is happy to be able to close the car's top quickly. This requires low-clearance multi-link hinges. The challenge with the aerodynamic components lies in their manufacture. In practice, the holes in the guides are only roughly punched, with a limited amount of fine cuts. In addition, there are rivets and plain bearings, which also have to operate without clearance throughout the entire system to avoid noise and rattling. Metallic rolled PTFE bearings have hit her to been the default, but they have to be recalibrated with great effort. This is where igus, the motion plastics specialist, comes into play with its plastic plain bearings, such as those made of the new iglidur F300material. "The disadvantage of plastic plain bearings - that they become soft at high temperatures - is an advantage here," explains Markus Feth, Head of Automotive at igus.
Self-calibration due to high temperatures
The bushing made of the iglidur F300 material is mounted with pretension in the bearing point. It undergoes cathodic dip painting, a process for even surface coating. For this, igus has developed the new iglidur F300 material to be electrically conductive so that it doesn't insulate the individual parts of the hinge from one another. The conductivity is designed to be sufficient for a good coating result. However, the igus bearings are more insulating than metal plain bearings, so there is no significant corrosion in the usual OEM salt spray and climate change tests. This is especially important for aero dynamic components, such as spoiler kinematics and adjustable diffusers. The material is also extremely wear-resistant and withstands the special thermal requirements of the subsequent burning process. The bearing recalibrates itself during the drying process at 180 to 220 degrees. Despite roughly punched holes and cold-bolt extrusion, the customer thus receives a low-clearance bearing that operates smoothly.
Find out more about the new iglidur F300 plain bearing at: https://www.igus.eu/info/iglidur-f300-plain-bearings-for-cathodic-dip-painting.
ABOUT IGUS:
igus GmbH develops and produces motion plastics. These lubrication-free, high-performance polymers improve technology and reduce costs wherever things move. In energy supplies, highly flexible cables, plain and linear bearings a swell as lead screw technology made of tribo-polymers, igus is the worldwide market leader. The family-run company based in Cologne, Germany, is represented in 31 countries and employs 4,900 people across the globe. In 2021, igus generated a turnover of €961 million. Research in the industry's largest test laboratories constantly yields innovations and more security for users. 234,000articles are available from stock and the service life can be calculated online. In recent years, the company has expanded by creating internal startups, e.g. for ball bearings, robot drives, 3D printing, the RBTX platform for Lean Robotics and intelligent "smart plastics" for Industry 4.0.Among the most important environmental investments are the "chainge" programme – recycling of used e-chains - and the participation in an enterprise that produces oil from plastic waste.