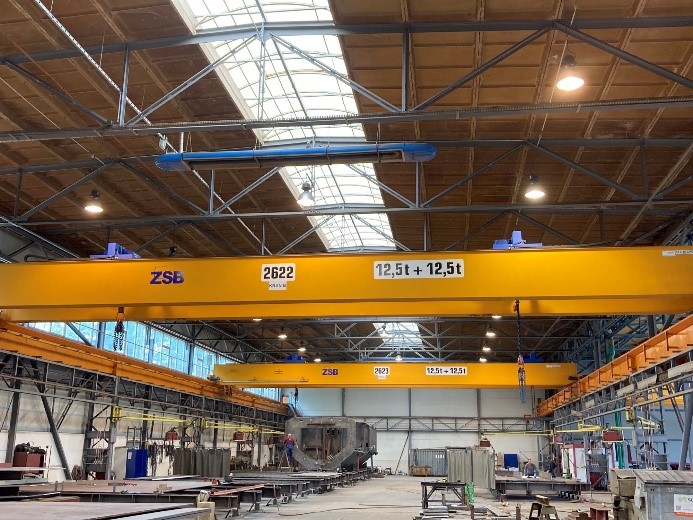
Steel cable instead of trough – new energy supply for a BANG crane
BANG Kransysteme GmbH & Co. KG, based in Oelsnitz/Vogtland, enjoys success throughout Europe with its process cranes and special cranes. The cranes deliver top-flight performance in such areas as the steel industry, automotive industry pressing plants and nuclear power plants. With a current project, the company is showing that it can also do standard things - and then go beyond the standard in a very flexible way when necessary. That is why the new ZSB Zwickauer Sonderstahlbau GmbH gantry crane uses the igus autoglide 5 energy chain.
The energy chains that BANG requested from igus were actually supposed to be "completely normal" ones. The BANG engineers working for ZSB Zwickauer Sonderstahlbau GmbH had planned a project for two identical cranes for steel plate handling. The 22.5-metre bridges, each with a 12.5-tonne hoist, were to be equipped with a component kit (drives, wire rope, energy supply) from a German manufacturer. BANG doesn't usually implement projects like standard cranes for handling tasks.
Most BANG cranes are process cranes with application-specific designs and a great deal of vertical integration in construction. This creates the conditions for cranes to perform their lifting tasks for many years, especially under extreme conditions – reliably, precisely and safely. The load suspension devices are often complex custom-made products.
Energy supply to electromagnets
For one of the two cranes, however, the energy supply that was part of the standard package could not be used. Florian Pletz, Head of Service and After-Sales and project officer for standard cranes at BANG, says, "If it needs to, this crane can use an electromagnet instead of a hook. So it requires an enhanced power supply all the way to the load suspension device and therefore a larger energy chain." And that is what BANG requested from igus. Exactly at that time, the igus Industry Manager for cranes, Theo Diehl, had a conversation with BANG and mentioned a new development: the autogilde 5 energy chain. Two days later, BANG modified its request to read "Please send us a quotation for the autoglide 5 – we need all the space we can get."
The art of elimination: steel cable guide instead of trough
igus developed the autoglide 5 for such applications. Theo Diehl describes the starting point for the development. "We asked ourselves: what can we eliminate? Not the cables, not the chain – but maybe the trough." The trough is replaced with a steel cable that is stretched across the substructure. The cable also engages in the chain's guide elements, guiding the chain reliably. The result is a new guide system that takes up hardly any space, and that is just what BANG needed.
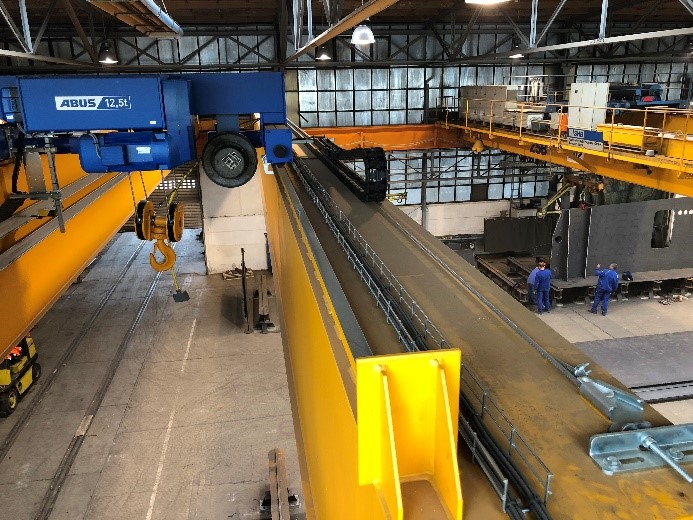
Pletz says, "On the top belt, for instance, we needed a trolley, and we needed safety clearance to avoid pinch points." And they got it with the autoglide 5, which is the epitome of the igus design principle. Says Diehl, "Our goal is always to let the crane determine the installation space and to design the chain to fit within that structure." The autoglide 5 was developed for indoor cranes and storage and retrieval units with travels of up to 80 metres. The users of this system save space, installation time and cost. That is why the new energy supply received interest immediately, and not just from BANG, but from users looking for a low-wear alternative to busbar systems.
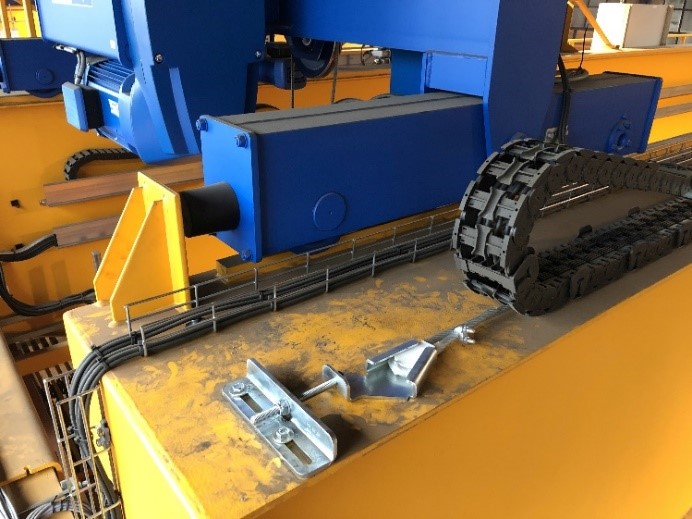
Special solution for two reverse chains
The autoglide 5 energy chain on the crane is well filled. The trolley's primary power supply alone requires five individual cores with a cross section of four square millimetres. But to use the autoglide 5 for this project, igus had to implement a special solution. igus sales consultant Denny Woogk says, "The default for the autoglide 5 is end infeed. But since two moving trolleys had to be supplied with power here, we needed two reverse chains with a common guide." This little problem was solved with a customised fixed-end bridge that igus manufactured with 3D printing – the first autoglide 5 with reverse supply. This shows that igus project work is just as flexible and adaptable to special requests as BANG is.
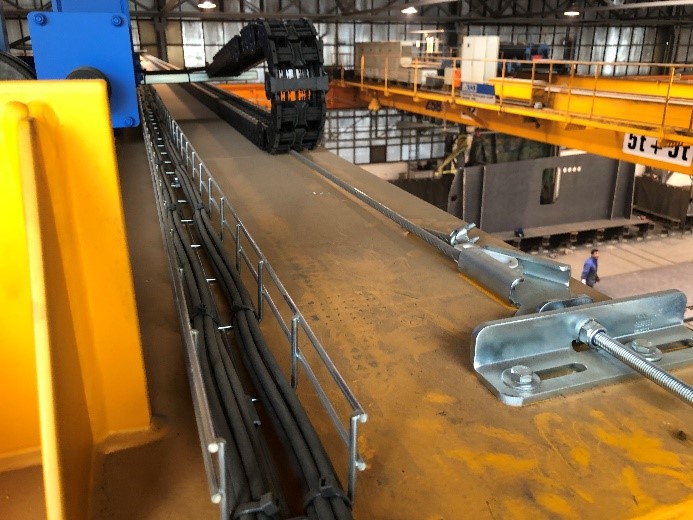
Conclusion: flexible standard crane, innovative energy supply system
The cranes have now been installed at one of ZSB Zwickauer Sonderstahlbau GmbH's new construction sites. Peter Knösel, Head of Project Management and Sales: "We are very pleased with both the cranes and the project process, and the new troughless energy chain has proven very effective." ZSB is a well-known specialist for steel bridge construction, covering the most commonly used construction methods, from box girders to framework structures and tied arch bridges to pylons.
Its 155 employees process more than 1,000 tonnes of steel each month. Individual components can be up to 60 metres long and weigh up to 200 tonnes, and some projects involve welding 4,000 to 10,000 tonnes of steel into bridge constructions. Another ZSB speciality is the manufacture of construction machinery components weighing up to 100 tonnes. These components made of special steels are used in large excavators for opencast mining. The new ZSB cranes are at the very beginning of the process chain. Among their tasks is feeding the cutting system with steel plates and handling steel constructions. And the cranes are very flexible. They can also be used in a tandem lift with all four hoists (via a single radio remote control).
ABOUT IGUS:
igus GmbH develops and produces motion plastics. These lubrication-free, high-performance polymers improve technology and reduce costs wherever things move. In energy supplies, highly flexible cables, plain and linear bearings as well as lead screw technology made of tribo-polymers, igus is the worldwide market leader. The family-run company based in Cologne, Germany, is represented in 35 countries and employs 3,800 people across the globe.
In 2019, igus generated a turnover of €764 million. Research in the industry's largest test laboratories constantly yields innovations and more security for users. 234,000 articles are available from stock and the service life can be calculated online. In recent years, the company has expanded by creating internal startups, e.g. for ball bearings, robot drives, 3D printing, the RBTX platform for Lean Robotics and intelligent "smart plastics" for Industry 4.0. Among the most important environmental investments are the "chainge" programme – recycling of used e-chains - and the participation in an enterprise that produces oil from plastic waste. (Plastic2Oil).