How polymer knife edge rollers are making maintenance-free conveyor belts and packaging systems possible, enhancing performance.
Krones AG produces systems and machines for making, filling and packaging beverages and liquid food. The industry never sleeps. So it is hardly surprising that Krones systems have to break their own speed records again and again. This becomes a problem when apart cannot withstand the pressure and there is no alternative that can perform better. That is why igus GmbH developed knife edge rollers made of tribo-polymers for Krones, helping them achieve new records.
In 2005, Krones faced a challenge with the Variopac Pro, a fully automatic all-round packaging system: the system's performance had to be increased by 20 packs per minute. There was therefore an urgent need to change the conveyor belt deflection. Originally, metal rollers with needle roller bearings were used here, but they couldn't meet the higher performance requirements and were cost-intensive. Looking for an alternative, Krones DesignEngineer Jürgen Werner came upon igus GmbH products.
Continuous operation, sugar, heat and no solution in sight?
The Variopac Pro processes cans and glass or PET bottles that hold between 0.2 and 5 litres, packaging them in boxes or wrapping them in film. Components must meet stringent requirements, since the system is in continuous operation. "This means that our end customers run our systems round the clock. Sometimes sugar particles can be found in the surroundings due to production, and they abrade moving machine components much as sandpaper would. This happens at belt speeds of up to 0.9m/s", Werner says in an interview.Dust, sand and moisture are business as usual wherever the Variopac Pro is used. But that is not all. Right at the system's shrink tunnel, conveyor belts are continuously exposed to temperatures of up to 100°C. Despite the se environmental conditions and the performance requirements, the new solution ford effecting the conveyor belts should have a service life of at least one year.
So the requirements of the desired products for reworking the knife edges were clear. But there was a different problem: a product that could meet these performance requirements did not exist. Searching for suitable experts, Krones AG came across igus. "We knew right away that we wanted to develop a solution with Krones. Even though our iglidur high-performance polymers were generally developed to guarantee low wear and friction, we were not at all sure at first that they could handle conditions in the Variopac Pro", recalls Lars Braun, igus Packaging Industry Manager.
igus and Krones worked together to develop aworking solution
In working with Krones AG to reach the desired result, igus tested various approaches in its test laboratory before they were used in the Variopac Pro. The first approach was thin-walled metal tubes into which iglidur plain bearings were pressed. This proved too expensive and labour-intensive, since each plain bearing had to be inserted into the tubes separately. So igus kept tinkering until the knife edge roller was developed. It was an injection-moulded solid plastic roller made of a material developed specifically for this application. "The pv values in the Krones systems were very high even then. So we had to make sure that our knife edge rollers could handle these loads and were suitable for use as a series product", Braun explains.
The best test results were achieved with the material iglidur P210. This is characterised by its high wear resistance, low coefficient of friction and the resulting low drive power of the conveyor belts. Like all iglidur materials, it is suitable for maintenance-free and lubrication-free operations. Because it can also be used in a variety of applications, this material fulfilled all requirements. When it was clear that knife edge rollers made of iglidur P210 far exceeded the required one-year service life, Krones decided to install them in the Variopac Pro. "Our systems are used around the world, and they do not fail. The iglidur knife edge rollers simply work and have hardly any noticeable wear. They are also easy to install and save our customers time-consuming maintenance", says Werner.
Safe product transport at any belt speed
Krones now installs iglidurknife edge rollers in the Variopac Pro wherever there is a transition between two conveyor belts or plastic modular chains. Because the knife edge roller diameters are small, conveyor belts and modular chains can be deflected very close together, so the gap between two belts is very small. Things that sound banal are extremely important in beverage production. If beverage containers tip during the transition from one belt to the next because the gap is too large, the result could be massive production losses and costly, time-consuming cleaning. A belt that is too slow increases this risk.
"If, for example, beverages containing sugar are being packaged, the cleaning cost and effort is immense if containers tip over and break. Even if the system operates at low speed, iglidur knife edge rollers enable us to prevent tipping. This allows even star-bottom bottles, which are susceptible to tipping, to be packaged without any trouble", Werner says. The faster the belt travels, the lower the risk of beverage containers tipping. But because the Variopac Pro is very flexible, it must function as reliably at 150 packages per minute as at 20. The same is true of moving components, and for the iglidur knife edge rollers.
Environment and speed play an important role
According to Werner, various future trends can be identified in the packaging industry. One is that the roles of packaging sizes and environmental protection are increasing in importance. Product and container sizes are increasing in order to reduce packaging waste. "We're talking about up to 45 bottles, each holding 0.5 litres, per package. This leads to great weight and high loads for our systems and for the knife edge rollers", explains Werner. System speed will continue to increase. Currently, a knife edge roller's running performance in the Variopac Pro is up to 11,000 kilometres per year given a belt speed of 0.34m/s. "Speeds of this magnitude are no problem for iglidur P210 knife edge rollers. We have tested speeds of up to 1m/s in our test laboratory. We continuously work on refining our products and materials so that we can meet new challenges in the future", says Braun.
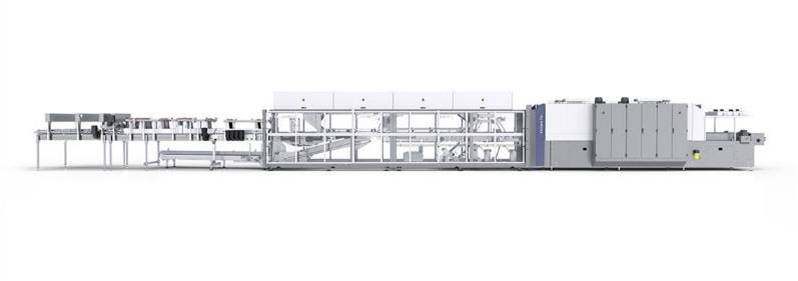
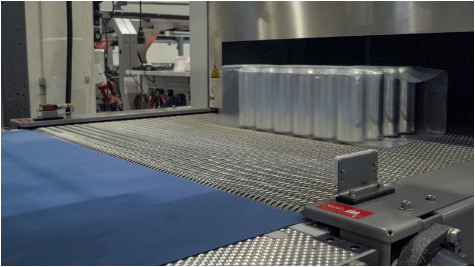
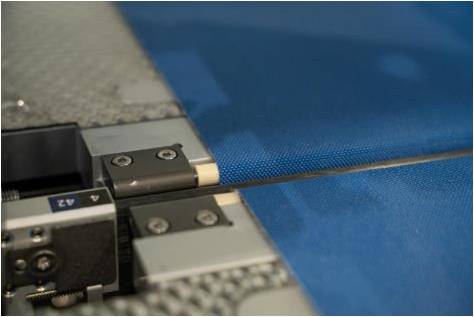
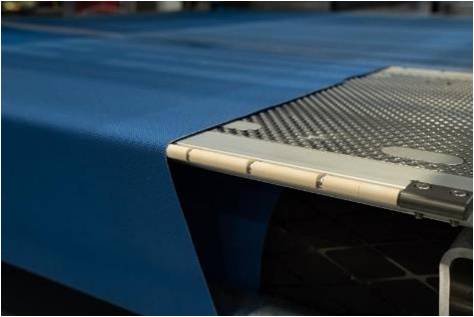
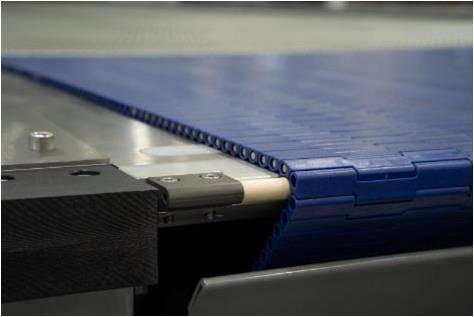